Solving the Puzzle: Step-by-Step Well Pump Troubleshooting Guide
Home >
Well Pump Replacement Basics
Understanding the basics of well pump replacement is essential for homeowners in New Hampshire. Being aware of the signs of well pump issues and the importance of timely replacement can save time, money, and ensure a continuous water supply.
Signs of Well Pump Issues
Recognizing the early warning signs of well pump problems can help homeowners take prompt action. Some common indications that a well pump may need replacement include:
- No Water or Low Water Pressure: If faucets are running dry or water pressure is significantly reduced, it could be a sign of a failing well pump (Water Well Journal).
- Strange Noises: Unusual sounds such as grinding or clicking coming from the pump can indicate mechanical issues (National Ground Water Association).
- Air Spitting from Faucets: Air mixed with water coming from faucets could point to a problem with the well pump or a drop in the water level.
- Constant Running: If the pump is running continuously without shutting off, it may be struggling to maintain pressure due to a malfunction (Well Owner).
For more detailed information, visit our article on signs of well pump failure.
Importance of Timely Replacement
Timely well pump replacement is crucial for several reasons:
- Preventing Water Supply Interruption: A fully functional well pump ensures a continuous water supply for household needs. Delaying replacement can lead to complete pump failure and significant inconvenience (Water Systems Council).
- Avoiding Costly Repairs: Replacing a failing well pump promptly can prevent further damage to the well system, which can be more expensive to repair than the pump itself.
- Maintaining Water Quality: A malfunctioning pump can lead to contamination or sediment in the water supply, affecting water quality (National Ground Water Association).
- Energy Efficiency: A well-functioning pump operates more efficiently, reducing energy consumption and saving on utility bills.
Issue | Consequence |
---|---|
No Water/Low Pressure | Interrupted water supply |
Strange Noises | Potential mechanical failure |
Air Spitting | Possible drop in water level |
Constant Running | Increased energy use |
For more insights into the process, check out our guide on well pump replacement near me.
Understanding these basics can help New Hampshire homeowners take proactive steps in maintaining their well systems. For further details on related topics, including cost considerations and types of well pumps, explore our comprehensive well pump troubleshooting guide.
Hiring a Professional
Finding Reliable Service Providers
When it comes to well pump troubleshooting and replacement, finding a reliable service provider is crucial for ensuring a successful and efficient job. Below are some key steps to help you find a trustworthy professional:
- Check Credentials and Certifications: According to the American Ground Water Trust, it is essential to verify the credentials and certifications of well pump professionals. Ensure they are licensed and bonded, which guarantees they meet industry standards and have undergone necessary training.
- Seek Recommendations: The Environmental Protection Agency advises checking with local well drilling companies for recommendations. They often have insights into reputable service providers in your area.
- Review Experience and Training: As noted by WellOwner.org, inquire about the experience and training of service providers. Experienced professionals are more likely to handle complex issues effectively.
- Check Reviews and References: Look for reviews online and ask for references from previous clients. This can provide a sense of the service provider’s reliability and quality of work.
- Verify Insurance and Bonding: Ensure the service provider has proper insurance and bonding. This protects you from any liability in case of accidents or damage during the well pump replacement process.
Questions to Ask Before Hiring
Asking the right questions can help you determine if a service provider is the right fit for your well pump troubleshooting and replacement needs. Here are some important questions to consider:
- What is your level of experience with well pump replacements?
- Knowing their experience can give you confidence in their ability to handle your specific issue.
- Are you licensed and bonded?
- Verify their credentials to ensure they are qualified for the job.
- Can you provide references?
- Speaking with previous clients can offer insights into their service quality and reliability.
- What is your availability?
- Ensure their schedule aligns with your needs, especially if it’s an urgent replacement.
- What are your service rates?
- Understanding their pricing can help you budget appropriately. For more details on costs, visit our section on well pump replacement cost.
- Do you offer a warranty on your services?
- A warranty can provide peace of mind, knowing that any issues post-replacement will be addressed.
- What safety measures do you take?
- Ensuring they follow safety protocols is critical, especially when dealing with water systems.
- Do you have experience with the specific type of well pump I have?
- Whether it’s a submersible well pump replacement or a deep well pump replacement, ensure they have relevant experience.
By asking these questions and following the steps to find reliable service providers, New Hampshire homeowners can ensure a smooth and effective well pump troubleshooting and replacement process. For more detailed guidance, visit our articles on signs of well pump failure and well pump replacement parts.
Types of Well Pumps
When approaching well pump troubleshooting, understanding the types of well pumps is crucial. There are two primary types of well pumps used in residential settings: submersible well pumps and jet well pumps. Each type has its own characteristics and is suitable for different applications.
Submersible Well Pumps
Submersible well pumps are installed underwater, typically within the well itself. These pumps are designed to push water to the surface, making them highly efficient and effective for deep wells. A key advantage of submersible pumps is their ability to operate quietly since they are submerged.
Submersible Well Pumps | Characteristics |
---|---|
Installation Depth | Up to 400 feet |
Efficiency | High |
Noise Level | Low (underwater operation) |
Maintenance | Requires pulling the pump from the well |
For more detailed information on replacing submersible well pumps, check our guide on submersible well pump replacement.
Jet Well Pumps
Jet well pumps, on the other hand, are installed above ground. These pumps use a combination of suction and pressure to draw water from the well. Jet pumps are divided into two categories: shallow well jet pumps and deep well jet pumps. Shallow well jet pumps are suitable for wells up to 25 feet deep, while deep well jet pumps can handle depths up to 100 feet.
Jet Well Pumps | Characteristics |
---|---|
Shallow Well Jet Pumps | Suitable for wells up to 25 feet |
Deep Well Jet Pumps | Suitable for wells up to 100 feet |
Installation | Above ground |
Maintenance | Easier access for repairs |
For more on replacing jet well pumps, visit our page on shallow well pump replacement.
Understanding these types of well pumps can aid in troubleshooting and determining the best replacement option for your specific needs. For further insights into well pump issues and their signs, refer to our article on signs of well pump failure, and for cost considerations, visit well pump replacement cost. If you need professional assistance, check our guide on finding well pump replacement near me.
Cost Considerations
Factors Affecting Replacement Cost
When considering the cost of well pump replacement, several factors come into play. Understanding these variables can help homeowners in New Hampshire make informed decisions and prepare financially for the process.
- Type of Well Pump: The type of pump—whether submersible, jet, or another variety—affects the cost. Submersible pumps tend to be more expensive due to their complexity and installation depth. For more information, see our section on submersible well pumps.
- Depth of the Well: The depth of the well influences the cost significantly. Deeper wells require more powerful pumps, which are typically more expensive. For details on replacing deep well pumps, visit deep well pump replacement.
- Pump Capacity: The capacity of the pump, measured in gallons per minute (GPM), also impacts the cost. Higher capacity pumps are generally more expensive.
- Labor Costs: Labor costs can vary depending on the complexity of the installation and the rates of local service providers. It’s essential to get multiple quotes from reliable service providers.
- Additional Components: Replacement may require additional parts such as pressure tanks, control boxes, or wiring. Visit well pump replacement parts for more details.
- Permits and Inspections: Some regions may require permits and inspections, adding to the overall cost.
Factor | Cost Impact |
---|---|
Type of Well Pump | High |
Depth of the Well | High |
Pump Capacity | Medium |
Labor Costs | Variable |
Additional Components | Medium |
Permits and Inspections | Variable |
Budgeting for Well Pump Replacement
Budgeting for well pump replacement requires careful planning and consideration of the factors mentioned above. Here are some tips to help New Hampshire homeowners budget effectively:
- Get Multiple Quotes: Obtain quotes from several professionals to compare prices and services. This can help you find the best deal without compromising on quality. Check out finding reliable service providers for more guidance.
- Consider Financing Options: Some companies offer financing options or payment plans, making the cost more manageable over time.
- Set Aside an Emergency Fund: Having an emergency fund can help cover unexpected costs that may arise during the replacement process.
- Prioritize Necessary Components: Focus on essential components first and consider upgrading additional parts later if the budget allows.
- Regular Maintenance: Regular maintenance can extend the average lifespan of a well pump, potentially delaying the need for replacement and saving money in the long run.
For more detailed budgeting tips, visit Budgeting Tips for Well Pump Replacement.
By understanding the factors that affect the cost of well pump replacement and following these budgeting tips, homeowners can better prepare for the financial aspects of the process. For additional information on troubleshooting well pumps, see our section on DIY well pump replacement.
DIY Troubleshooting Tips
For New Hampshire homeowners, dealing with well pump issues can be a daunting task. However, understanding basic troubleshooting steps can help identify and possibly resolve some common problems before calling in a professional.
Basic Checks and Maintenance
Before jumping to conclusions, it’s crucial to perform some basic checks and maintenance on your well pump system. These steps can often resolve minor issues and prevent more severe problems.
- Check the Power Supply:
- Ensure the well pump is receiving power. Check the circuit breaker and reset it if necessary.
- Inspect any fuses and replace if blown.
- Inspect the Pressure Switch:
- The pressure switch regulates the activation of the well pump. Ensure it is functioning correctly by checking for any visible signs of damage or wear.
- Clean any debris or insects that might obstruct the switch.
- Examine the Pressure Tank:
- Check the pressure tank for proper pressure levels. The tank should have an air charge of approximately 2 psi below the cut-in pressure of the pump.
- Tap the tank; a hollow sound indicates it is functioning correctly, while a dull sound may suggest waterlogging.
- Inspect for Leaks:
- Visually inspect the entire system for any signs of leaks.
- Check all fittings, pipes, and connections.
- Test the Pump Motor:
- Listen for unusual noises from the pump motor, such as humming or grinding.
- Check the motor’s temperature; an overheating motor may indicate a problem.
Common Issues | Possible Solutions |
---|---|
No water flow | Check power supply, inspect pressure switch |
Low water pressure | Examine pressure tank, inspect for leaks |
Pump cycling on and off | Test the pump motor, check pressure switch |
For further details on understanding common issues, visit our guide on signs of well pump failure.
When to Call a Professional
While basic checks and maintenance can resolve minor issues, some situations necessitate the expertise of a professional. Knowing when to call for help can save time and prevent further damage.
- Persistent Low Water Pressure:
- If low water pressure persists despite basic troubleshooting, it could indicate a deeper issue such as a failing pump or a problem with the well itself.
- Persistent issues may require a submersible well pump replacement or evaluation of the well’s condition.
- Unusual Noises:
- Grinding, screeching, or other unusual noises from the pump motor could indicate mechanical failure.
- Professionals can diagnose and replace damaged components accurately.
- Frequent Pump Cycling:
- If the pump cycles on and off frequently, it may indicate a pressure switch malfunction, a waterlogged tank, or other underlying issues.
- Professional assessment can identify the root cause and provide the appropriate solution.
- No Water Flow:
- Complete loss of water flow could be due to a failed pump, electrical issues, or problems with the well.
- A professional can perform a comprehensive inspection and determine the necessary repairs or well pump replacement.
- Age and Wear:
- If the well pump is nearing the end of its lifespan, as detailed in our average lifespan of a well pump guide, it may be more cost-effective to replace the pump rather than perform repeated repairs.
For any complex issues or if you’re unsure about performing certain checks, it’s always best to consult with a professional to avoid causing further damage. For more information on hiring reliable service providers, visit our section on finding reliable service providers.
Understanding when to perform DIY troubleshooting and when to call a professional can ensure your well pump system remains functional and efficient, providing your home with a reliable water supply.
Understanding the Process
Steps of Well Pump Replacement
Replacing a well pump involves a series of methodical steps to ensure proper installation and functionality. Here is a clear and concise guide to the steps involved:
- Diagnose the Problem: Before initiating the replacement, verify that the well pump is indeed the issue. Check for signs of well pump failure like low water pressure, strange noises, or no water flow.
- Turn Off Power: Safety first. Ensure that the power supply to the well pump is completely shut off to avoid any electrical hazards.
- Remove the Well Cap: Carefully remove the well cap to access the pump. This might involve unscrewing bolts or fasteners.
- Disconnect the Pump: Disconnect the well pump from the piping and electrical connections. This can be a complex task and may require specific tools.
- Remove the Old Pump: Extract the old pump from the well. For submersible pumps, this could mean pulling the pump up from a significant depth (submersible well pump replacement).
- Install the New Pump: Place the new well pump into the well. Ensure that it is properly aligned and secured.
- Reconnect Piping and Electrical: Reattach the piping and electrical connections to the new pump. Make sure all connections are tight and secure to prevent leaks and electrical issues.
- Test the Pump: Turn the power back on and test the new pump. Check for consistent water flow, proper pressure, and any unusual noises.
- Seal the Well Cap: Once the pump is confirmed to be working correctly, replace and seal the well cap.
For those considering a DIY approach, it’s crucial to be familiar with the entire process and have the necessary tools and knowledge (DIY well pump replacement). However, hiring a professional might ensure a more efficient and safer replacement.
Post-Replacement Maintenance
Maintaining your well pump post-replacement is essential for ensuring its longevity and optimal performance. Here are some maintenance tips:
- Regular Inspections: Conduct regular visual inspections of the well pump system. Look for any signs of wear, corrosion, or leaks. Early detection can prevent major issues.
- Check Pressure Settings: Ensure that the pressure settings are correctly adjusted according to the manufacturer’s specifications. Incorrect pressure can lead to pump failure.
- Clean the Well Cap: Keep the well cap clean and free from debris. This prevents contaminants from entering the well.
- Monitor Water Quality: Regularly test the water quality from the well. Poor water quality can indicate problems within the well or the pump system.
- Service the Pump: Schedule periodic professional servicing to check for any underlying issues. A professional can perform in-depth inspections and maintenance tasks that might not be possible for a homeowner.
- Keep Records: Maintain a log of all maintenance activities, repairs, and replacements. This helps in tracking the performance and identifying any recurring issues.
- Use a Surge Protector: Protect your well pump from electrical surges by installing a surge protector. This can prevent damage from power fluctuations.
Maintenance Task | Frequency |
---|---|
Visual Inspection | Monthly |
Pressure Check | Quarterly |
Water Quality Testing | Annually |
Professional Servicing | Annually |
Record Keeping | Ongoing |
For more detailed information on well pump maintenance, visit well pump maintenance tips.
By understanding the process and adhering to a regular maintenance schedule, homeowners can ensure their well pump operates efficiently and lasts longer. For more information on well pump replacement and maintenance, check out our articles on well pump replacement cost and well pump replacement near me.
CONTACT US TODAY

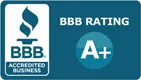

As Seen & Heard On
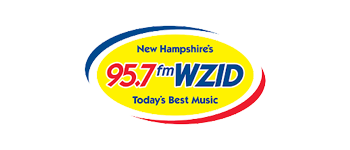
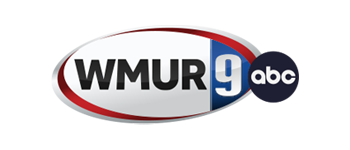

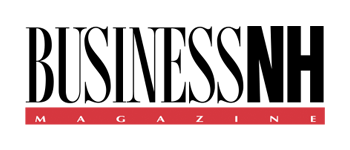
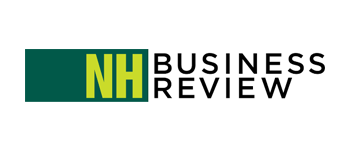
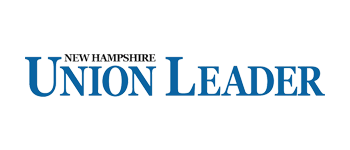
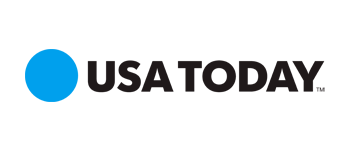
Reach Out to Our Team for More Details
Feel free to call Sanford Temperature Control or fill out the online form for more information. You may also get in touch with our team to schedule an appointment. We look forward to hearing from you.