Troubleshooting Made Easy: How to Fix Mitsubishi Ductless Mini Split E9 Error Code
Home >
Understanding Your Mini Split’s Language
When your Mitsubishi ductless mini split system presents an issue, it communicates through specific error codes, each detailing a unique problem. Learning to interpret these codes is vital in diagnosing and addressing the issue.
Deciphering Error Codes
Error codes on your Mitsubishi system are not just random combinations of letters and numbers; they are your unit’s way of indicating its health and any issues it may be experiencing. For instance, the mitsubishi ductless mini split e9 error code you’re encountering signals a specific problem that requires your attention.
The Mitsubishi ductless mini split systems display a range of error codes from E0 to E9, P1 to P9, and U1 to U8, each pointing to a particular type of malfunction. For example, the E9 error code is associated with a pressure sensor error or refrigerant leakage concern (PIONEER Official Store), while an E6 error could suggest an indoor/outdoor communication issue (212 HVAC).
Error Code | Issue |
---|---|
E9 | Pressure Sensor Error/Refrigerant Leakage |
E6 | Indoor/Outdoor Communication |
P8 | Overheating Issue |
E1 | Indoor PCB Error |
U4 | Outdoor Unit Communication |
For a comprehensive list of error codes and their meanings, you can refer to mitsubishi heat pump error codes and mitsubishi ductless mini split error codes. These resources will provide you with detailed explanations and the next steps to take.
When your mini split signals an error, it’s crucial to check the LED display on the outdoor controller board for insights on the malfunction. This will guide you in troubleshooting and determining whether you can apply a DIY fix or if professional assistance is necessary (troubleshooting mitsubishi ductless mini split error codes).
By acquainting yourself with these codes, you become better prepared to maintain your unit’s performance and address issues promptly. For a more in-depth guide on common error codes for Mitsubishi heat pumps and how to troubleshoot them, explore common error codes for mitsubishi heat pumps. Remember, a well-maintained system is less likely to encounter these errors, ensuring your comfort remains uninterrupted.
Identifying the E9 Error
When your Mitsubishi ductless mini split displays an E9 error code, it’s an alert that there’s an issue requiring your attention. Understanding the symptoms and performing initial checks can help you pinpoint the problem.
Symptoms and Initial Checks
The E9 error code usually indicates that the unit’s indoor fan motor is not operating correctly. Symptoms may include the indoor unit failing to blow air or making unusual noises. Before diving into more advanced troubleshooting, there are a few things you can check:
- Power Supply: Ensure that the unit is receiving power. Check your circuit breaker or fuse box for any tripped breakers or blown fuses.
- Remote Control: Verify that the error code is indeed ‘E9’. Sometimes, a simple mistake in reading the display can send you on a wild goose chase.
- Visual Inspection: Look for any obvious signs of damage or blockages that could be affecting the fan motor’s operation.
- Error Code History: If your unit has a history of error codes, it might provide a clue to the underlying issue. Review the unit’s error code log if available.
After these initial checks, if the problem persists, it’s time to investigate possible causes for the E9 error code, such as fan motor issues, pressure sensor errors, or refrigerant leakage concerns. Further details on these potential causes can be found in our section on troubleshooting mitsubishi ductless mini split error codes.
If you suspect the problem is related to refrigerant leakage or a pressure sensor malfunction, which are also common culprits for the E9 error code (Mitsubishi Electric UK), it is recommended to seek professional help due to the complexity of the HVAC system.
For additional information on Mitsubishi ductless mini split error codes and how to address them, please refer to our comprehensive articles on mitsubishi heat pump error codes and mitsubishi ductless mini split error codes. If you’re encountering different error codes, such as the mitsubishi ductless mini split e6 error code or mitsubishi ductless mini split p8 error code, our guides provide tailored advice for each specific scenario.
Investigating the Causes
When your Mitsubishi ductless mini split displays the E9 error code, it’s signaling a specific issue that requires your attention. Understanding the potential causes behind this error code is the first step toward resolving the problem. Let’s delve into the common issues associated with the E9 error, which include fan motor issues, pressure sensor errors, and refrigerant leakage concerns.
Fan Motor Issues
The E9 error code often points to a malfunction concerning the indoor fan motor. If the fan motor isn’t operating correctly, your mini split system won’t be able to circulate air properly, leading to inefficient cooling and heating. Possible reasons for fan motor malfunctions include:
- A faulty fan motor: It might be damaged or have reached the end of its lifespan.
- Control board issues: A problem with the control board can disrupt the power supply to the fan motor.
- Wiring complications: Loose or damaged wiring can cause connectivity issues with the fan motor.
To pinpoint the issue, you’ll need to perform a thorough inspection. Begin by visually checking for any signs of damage or wear on the fan motor. Test the motor’s electrical connections for continuity with a multimeter, and examine the control board for any visible signs of damage like burn marks or bulging capacitors. If you’re unsure about handling electrical components, it’s wise to call a professional.
Pressure Sensor Errors
The E9 error can also indicate a pressure sensor fault. The pressure sensor monitors the refrigerant pressure within your mini split system to ensure it operates within safe limits. When a pressure sensor error occurs, consider the following:
- Check the sensor for blockages or physical damage that might interfere with its operation.
- Ensure the sensor is properly connected and the wiring is intact.
- Verify if the sensor readings are within the specified range for your unit.
To address these issues, you can consult the service manual for your specific model to understand the normal operating range and compare it to the current sensor readings. If you find a discrepancy, the sensor might need to be cleaned or replaced. For more information on this error and others, explore the common error codes for Mitsubishi heat pumps.
Refrigerant Leakage Concerns
An E9 error may also be a warning sign of refrigerant leakage or low pressure within the system. Refrigerant is the lifeblood of your mini split, and any loss can significantly impact performance. Key signs of refrigerant issues include:
- Ice buildup on the refrigerant lines or coils.
- Hissing sounds which may indicate a leak.
- A noticeable decrease in cooling or heating effectiveness.
To resolve refrigerant leakage, you must first locate the source of the leak, which may require a specialized detection tool or the expertise of a technician. Once identified, the leak must be repaired, and the refrigerant must be recharged to the manufacturer’s specifications. Handling refrigerant requires specific skills and tools, and in many areas, it’s regulated by law. If you suspect a refrigerant issue, it may be best to seek professional assistance.
In conclusion, the E9 error code is a critical alert from your Mitsubishi ductless mini split indicating that it’s time to investigate and address specific issues with the system. Whether it’s a fan motor problem, pressure sensor error, or refrigerant leakage, taking the appropriate steps to diagnose and fix the issue will ensure your unit returns to optimal operation. For more troubleshooting guidance, refer to the troubleshooting Mitsubishi ductless mini split error codes page.
Step-by-Step Troubleshooting
Addressing the Mitsubishi ductless mini split E9 error code requires a systematic approach. This step-by-step troubleshooting guide will help you identify the potential causes and find solutions.
Checking the Fan Motor
The E9 error code often points to issues with the indoor fan motor, which may not be working properly. Here’s how you can check the fan motor:
- Power Off: Ensure your safety by turning off the power to your mini split system.
- Access the Fan: Open the indoor unit’s front panel to access the fan motor. Refer to your user manual for specific instructions on how to do this.
- Visual Inspection: Look for any signs of damage or obstruction that might prevent the fan from spinning freely.
- Connectivity Test: Use a multimeter to check for continuity in the fan motor. If there’s no continuity, the fan motor may need to be replaced.
If you find the fan motor to be faulty, consider replacing it. If you’re not comfortable performing these checks, it may be time to call a professional.
Inspecting the Control Board
The control board is the brain of your mini split. It regulates power and communication between different components. Here’s what to do:
- Power Off: Always start by turning off the power to avoid any electrical hazards.
- Locate the Control Board: Open the indoor unit and locate the control board, again referring to your manual for guidance.
- Inspect for Damage: Look for any signs of burn marks, corrosion, or other damage on the board.
- Check Connections: Ensure all wire harnesses are securely connected to the control board.
If you observe any damage, the control board might need replacing. In such cases, professional help is recommended unless you have experience with electrical components.
Assessing Wiring Connections
Faulty wiring can lead to a variety of issues, including the E9 error. To check the wiring connections:
- Power Off: Make sure your unit is turned off before you start inspecting any wiring.
- Examine Wiring: Check the wiring connecting the fan motor to the control board. Look for any loose connections, fraying, or signs of wear.
- Tightness of Connections: Make sure all connections are tight and secure. Loose connections can cause intermittent issues that may trigger error codes.
- Continuity Test: Use a multimeter to check the continuity of the wires. Lack of continuity indicates a break in the wire that needs fixing or replacing.
Addressing wiring issues may resolve the E9 error. However, if you’re unsure about handling electrical wiring, consider seeking professional intervention.
By following these steps, you can troubleshoot and potentially fix the E9 error code on your Mitsubishi ductless mini split. If these solutions do not resolve the issue, or if you’re not comfortable performing them, it’s important to contact a licensed HVAC technician for assistance. Regular maintenance can also prevent future errors and ensure your system operates efficiently. For more information on common error codes for Mitsubishi heat pumps, explore our resources on common error codes for Mitsubishi heat pumps.
Professional Intervention or DIY
When confronted with a ‘mitsubishi ductless mini split e9 error code,’ you might wonder whether it’s a problem you can tackle on your own or if it’s time to call in the pros. Making the right decision here is crucial for the safety and functionality of your mini split system.
When to Call a Pro
If you’ve gone through the steps in our troubleshooting mitsubishi ductless mini split error codes guide and the E9 error persists, it might be time to seek professional help. Here are scenarios when you should definitely call a professional:
- Electrical Issues: If your troubleshooting indicates a problem with electrical components or internal wiring, it’s safer to let a licensed technician handle it. Handling electrical components without proper training can be dangerous and could lead to further damage.
- Persistent Error Codes: If the E9 error code continues to display after you’ve performed basic checks and resets, a deeper issue may be at play. A professional service engineer can conduct a thorough diagnosis to identify and fix the problem.
- Pressure Sensor Errors: While you may be able to check the pressure sensor for blockages or disconnections, if you’re unsure of how to safely access or assess the sensor, it’s best to call a professional. An incorrect assessment could lead to incorrect pressure levels, which could damage your system.
- Refrigerant Handling: Dealing with refrigerant requires specialized knowledge and tools. If you suspect that your E9 error is due to refrigerant leakage or pressure issues, a certified HVAC technician should handle the repair to comply with safety regulations and environmental laws.
In any of these situations, it’s crucial to choose a reputable HVAC professional who is experienced with mitsubishi heat pump error codes and can provide reliable service.
DIY Repair Tips
Before you decide to call a pro, here are some DIY repair tips that might resolve the E9 error code:
- Check for Obvious Blockages: Sometimes, the error could be caused by something as simple as a blockage in the system’s air filters or vents. Ensure these are clean and clear.
- Reset the System: Occasionally, a simple system reset can clear error codes. Turn off the power to your mini split for a few minutes, then turn it back on and check if the error persists.
- Check Connections: Ensure that all electrical connections are secure and that there are no loose wires. Refer to your mini split’s manual for guidance on how to safely check these connections.
- Sensor Check: If you’re comfortable and have the know-how, check the pressure sensor for any signs of damage or disconnection. However, if you’re uncertain, it’s better to avoid tampering with it.
While these tips can be helpful, never attempt any repairs that you’re not confident you can perform safely and correctly. Sometimes, the best DIY tip is knowing when not to DIY. If you’ve reached that point, it’s time to reach out to a professional who can provide the necessary service for your mitsubishi ductless mini split.
Remember, regular maintenance can prevent many issues from occurring in the first place. After resolving the E9 error, consider scheduling routine check-ups to keep your system running smoothly and to minimize the risk of future error codes.
Preventing Future E9 Errors
Maintaining the efficiency and longevity of your Mitsubishi ductless mini split is essential for a comfortable home environment. By implementing regular maintenance practices and applying early detection techniques, you can help prevent the recurrence of the mitsubishi ductless mini split E9 error code and other common issues.
Regular Maintenance Practices
Adopting a routine maintenance schedule is one of the most effective ways to avert potential problems with your mini split system. Here are several maintenance tips to keep your unit running smoothly:
- Clean or Replace Filters Regularly: Ensure the air filters are either cleaned or replaced every month or as recommended by the manufacturer to promote proper airflow and prevent overworking the system.
- Inspect and Clean the Outdoor Unit: Keep the outdoor compressor unit clear of debris, such as leaves and dirt, which can obstruct the fan and lead to overheating or other mechanical issues.
- Check Refrigerant Levels: Low refrigerant levels can trigger the E9 error code. Periodically verifying that refrigerant levels are within the recommended range is essential for the system’s proper functioning.
- Schedule Professional Inspections: Arrange for a certified HVAC technician to inspect your mini split system annually. They can conduct thorough checks and address any concerns before they escalate.
By following these maintenance practices, not only do you enhance the performance of your unit, but you also extend its lifespan, reducing the likelihood of facing an E9 error. Learn more about mitsubishi heat pump error codes and their maintenance requirements on our dedicated page.
Early Detection Techniques
Early detection of potential issues can save you from more significant problems down the line. Here are some techniques to help you catch issues early:
- Listen for Unusual Noises: Odd sounds coming from the indoor or outdoor unit can be a sign of mechanical troubles. Address these sounds promptly to avoid more serious complications.
- Monitor Cooling and Heating Efficiency: A noticeable drop in your mini split’s heating or cooling capacity could be a symptom of a developing issue.
- Watch for Error Codes: Familiarize yourself with common error codes for Mitsubishi heat pumps so you can identify problems early on. Quick recognition of error codes allows for prompt troubleshooting or professional assistance.
By incorporating these regular maintenance practices and early detection techniques, you’re much less likely to experience the E9 error again. Should an error arise, refer to our guides on troubleshooting mitsubishi ductless mini split error codes and other specific error codes such as E6, P8, E1, E0, and U4 to assist in resolving the issue.
CONTACT US TODAY

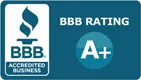

As Seen & Heard On
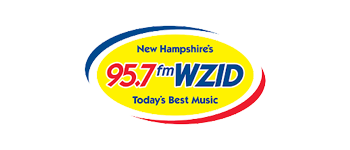
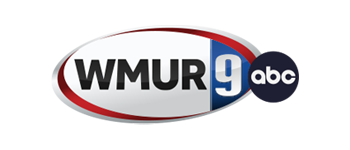

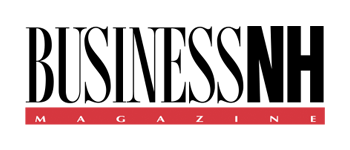
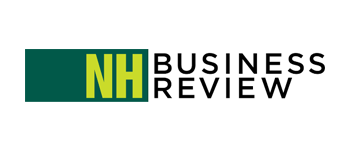
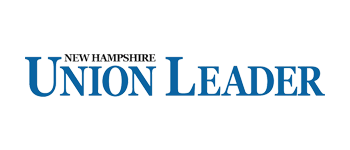
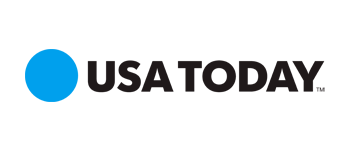
Reach Out to Our Team for More Details
Feel free to call Sanford Temperature Control or fill out the online form for more information. You may also get in touch with our team to schedule an appointment. We look forward to hearing from you.