Unlock the Secrets: Deciphering Common Error Codes for Mitsubishi Heat Pumps
Home >
Understanding Your Mitsubishi Heat Pump
Recognizing Error Codes
When your Mitsubishi heat pump exhibits an issue, it often communicates the problem through specific error codes. These codes appear as a combination of letters and numbers on your heat pump’s display panel or remote controller. Recognizing these error codes is the first step in diagnosing and resolving the issue with your heat pump system.
A list of common error codes for Mitsubishi heat pumps includes codes like E6, P8, E1, and U4, among others. Each code corresponds to a distinct issue within the heat pump system. For example, an E6 error code indicates a communication problem between the indoor and outdoor units, which could stem from various causes such as wiring or control board issues (JustAnswer).
To assist you in recognizing error codes, here’s a table with some of the common error codes you might encounter:
Error Code | Likely Issue |
---|---|
E6 | Communication error |
P8 | Overload issue |
E1 | Sensor error |
U4 | System malfunction |
Importance of Error Codes
Understanding and paying attention to the error codes displayed by your Mitsubishi heat pump is critical. These codes provide valuable insights into the health and functioning of your system. By decoding them, you can identify the root cause of the problem, which is essential for effective troubleshooting and repair.
Error codes serve as a preemptive warning that allows you to address issues before they escalate into major malfunctions or system failures. For instance, an E9 error code suggests a problem with the indoor fan motor, which, if left unattended, could lead to a complete breakdown of your unit.
Taking note of these error codes and understanding their implications can also save you time and money. In some cases, you might be able to perform simple fixes yourself, such as resetting the system or checking for loose connections. However, for more complex issues, these codes will help you communicate effectively with HVAC professionals when seeking repair services.
For a comprehensive list of error codes and their meanings, refer to our guide on mitsubishi ductless mini split error codes, and if you encounter a code that you’re not able to resolve, our article on troubleshooting mitsubishi ductless mini split error codes can help you with the next steps.
Common Mitsubishi Error Codes
When your Mitsubishi heat pump displays an error code, it’s signaling that there’s a specific issue that needs your attention. Understanding these error codes can be the key to quickly identifying and resolving problems with your system.
Communication Errors
Communication errors typically involve miscommunication between the indoor and outdoor units of your heat pump. A common error code you might encounter is E6, which suggests a communication fault. This could stem from improper wiring, a malfunctioning control board, or other connectivity issues that disrupt the communication flow. If you see the E6 error, it’s advisable to check the connections and, if the issue persists, seek professional help. For a comprehensive list of error codes, refer to our mitsubishi heat pump error codes page.
Error Code | Problem | Potential Solution |
---|---|---|
E6 | Communication Issue | Check wiring, consult a technician |
More details on this error can be found on mitsubishi ductless mini split e6 error code.
Fan Motor Issues
Fan motor issues can arise within both the indoor and outdoor units, and they are indicated by error codes such as E9 and E7. The E9 error code signals a problem with the indoor fan motor, which might include a faulty motor, wiring issues, or a defective control board. The E7 error code, on the other hand, points to an outdoor fan motor issue. Both require a thorough inspection of the fan system and possibly the assistance of a professional to diagnose and fix the underlying problem.
Error Code | Problem | Potential Solution |
---|---|---|
E9 | Indoor Fan Motor Problem | Inspect motor, check wiring |
E7 | Outdoor Fan Motor Problem | Inspect motor, check wiring |
For guidance on these issues, visit mitsubishi ductless mini split e9 error code and mitsubishi ductless mini split e7 error code, respectively.
Sensor and Temperature Errors
Your Mitsubishi heat pump relies on various sensors to monitor temperatures within the system. Errors like E4 indicate issues with these sensors, or the temperatures they detect. An E4 error code suggests a problem with the compressor, which may be due to a malfunctioning compressor, incorrect wiring, or a faulty control board. Check the sensors and wiring, and if you’re unable to resolve the issue, it’s time to contact an HVAC professional.
Error Code | Problem | Potential Solution |
---|---|---|
E4 | Compressor Problem | Check compressor, sensors, wiring |
Explore further details on mitsubishi ductless mini split e4 error code.
High-Pressure and Overload Issues
High-pressure and overload issues are serious and are typically indicated by the P8 error code. This code signifies that the system is experiencing an overload or that the pressure within the system is too high. This could be the result of a refrigerant issue, a blockage in the system, or a failing compressor. In such cases, it’s crucial to turn off your heat pump to prevent further damage and call a professional immediately.
Error Code | Problem | Potential Solution |
---|---|---|
P8 | High-Pressure/Overload | Turn off unit, consult a technician |
For additional information, check out mitsubishi ductless mini split p8 error code.
Understanding and deciphering these common error codes can help you diagnose issues quickly and take the appropriate steps towards resolution. For more detailed troubleshooting steps, see our guide on troubleshooting mitsubishi ductless mini split error codes. Remember, when in doubt, it’s best to call a professional to ensure your Mitsubishi heat pump returns to optimal functioning safely and effectively.
Troubleshooting Error Codes
When your Mitsubishi heat pump displays an error code, it’s signaling that it has diagnosed an issue within the system. Understanding and troubleshooting these codes can help you address the problem quickly and efficiently.
Initial Diagnostic Steps
If you encounter a common error code on your Mitsubishi heat pump, such as E6, which indicates a communication issue between the indoor and outdoor unit, here are some steps you can take before calling in a professional:
- Check the Power Supply: Ensure that your heat pump is receiving power and that no circuit breakers have been tripped.
- Inspect Wiring Connections: Faulty wiring can lead to communication errors like E0 and E6. Examine the connections between the indoor and outdoor units for any signs of damage or disconnection.
- Reset the System: Sometimes, a simple reset can clear the error code. Turn off the power to the unit, wait a few minutes, and then turn it back on.
- Clean or Replace Filters: Error codes such as E6 could also signify fan motor issues that might be resolved by cleaning or replacing air filters to ensure adequate airflow.
- Examine External Factors: Check for any external factors that could be causing the system to malfunction, such as obstructions around the units or extreme weather conditions.
By taking these initial diagnostic steps, you may be able to resolve common error codes such as E6, E9, or P8 without the need for professional assistance. For a comprehensive list of Mitsubishi heat pump error codes and their meanings, visit our detailed guide on mitsubishi heat pump error codes.
When to Call a Professional
There are certain situations where it’s best to call a professional for assistance:
- Persistent Error Codes: If the error code reappears after you’ve gone through the initial troubleshooting steps, it’s time to call a professional. Continuous error messages like E6 may indicate a more serious issue.
- Error Codes Indicating Sensor or Motor Issues: Error codes that point to sensor or motor problems, such as E9 for an indoor fan motor issue or P8 for a discharge temperature sensor malfunction, typically require technical expertise.
- Electrical Complications: If you suspect there are electrical issues, like wiring problems associated with error codes E0 or U4, it’s important to get a certified technician to handle these potentially dangerous situations.
- Error Codes You Don’t Understand: If you come across an error code that you cannot diagnose or resolve with the information available, such as E1 or E4, professional help is the safest option.
- When In Doubt: If you feel uncertain about any step in the troubleshooting process or if you are not comfortable handling HVAC equipment, it’s best to seek professional assistance. A certified technician can diagnose and resolve the issue, often more quickly and with less risk of further damage to the system.
Remember, regular maintenance and monitoring of your Mitsubishi heat pump can prevent many issues from occurring. For tips on maintaining your system, check out our article on regular maintenance tips. Calling a professional at the right time can save you from further inconvenience and ensure your heat pump operates efficiently.
Preventing Future Issues
Maintaining the efficiency and longevity of your Mitsubishi heat pump can save you from future troubles and unexpected breakdowns. Here are some regular maintenance tips and performance monitoring strategies to help prevent issues before they arise.
Regular Maintenance Tips
To keep your heat pump in top condition, it’s important to perform routine checks and maintenance tasks:
- Air Filter Maintenance: Your heat pump’s air filters are the first line of defense against dust and debris. Clean or replace them regularly to maintain proper airflow and prevent blockages. This simple step can prevent a multitude of common error codes for Mitsubishi heat pumps.
Maintenance Task Frequency Cleaning Filters Monthly Replacing Filters Every 3-6 Months Source: Valley Air Conditioning
- Outdoor Unit Inspection: Regularly inspect the outdoor unit and remove any debris, such as leaves or dirt, to ensure good airflow and prevent overheating.
- Refrigerant Level Check: Keep an eye on the refrigerant levels and ensure they are within the recommended range to maintain efficiency. If you notice levels dropping, it may indicate a leak, requiring professional intervention.
- Professional Maintenance: Schedule annual or bi-annual maintenance with a qualified technician. They can perform a comprehensive inspection, system cleaning, and preemptively address issues. Find more information about professional services on 212 HVAC.
Monitoring System Performance
Regularly monitoring your heat pump’s performance is key to early detection of potential issues:
- Temperature and Airflow: Keep track of the temperature and airflow. Any significant deviations from normal performance could indicate a problem. Consistency in these areas is a good sign of health.
- Energy Consumption: An unexpected increase in energy consumption can be a red flag. If your energy bills are rising without a clear explanation, it might be time to investigate your heat pump’s efficiency.
- Listen for Noises: Unfamiliar sounds coming from your heat pump could be a sign of mechanical issues. Paying attention to these cues can help you catch problems early.
- Error Code Awareness: Familiarize yourself with the meanings of Mitsubishi ductless mini split error codes. If an error code appears, refer to resources like troubleshooting Mitsubishi ductless mini split error codes for guidance.
By following these regular maintenance tips and monitoring your Mitsubishi heat pump’s performance, you can help prevent future issues, ensuring your system runs smoothly year-round. Remember, staying proactive with maintenance is the best strategy to avoid encountering error codes like E6, P8, E1, E9, E0, and U4.
CONTACT US TODAY

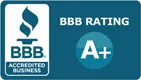

As Seen & Heard On
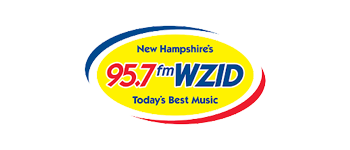
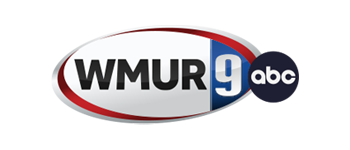

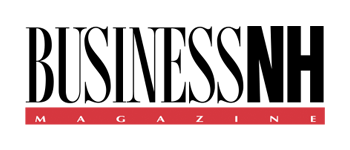
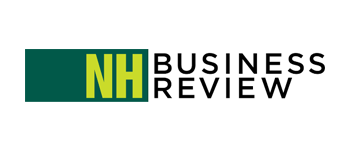
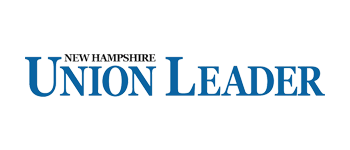
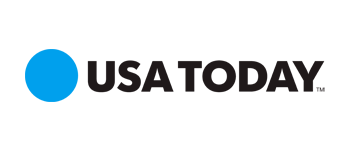
Reach Out to Our Team for More Details
Feel free to call Sanford Temperature Control or fill out the online form for more information. You may also get in touch with our team to schedule an appointment. We look forward to hearing from you.