Decode the Mystery: Troubleshooting Mitsubishi Ductless Mini Split Error Codes
Home >
Understanding Error Codes
When your Mitsubishi ductless mini split encounters issues, it communicates through specific error codes. These codes are your first clue when troubleshooting Mitsubishi ductless mini split error codes. Understanding what these codes mean can help you identify the problem and determine the best course of action.
Decoding the Codes
Error codes on your Mitsubishi ductless mini split system are alphanumeric and relate to particular problems with your unit. For instance, you might encounter codes like P1, E6, or U4, each indicating a different issue. The Mitsubishi Electric Error code search tool is an invaluable resource that provides information on the cause of the malfunction by simply entering the error code.
Here’s a brief overview of what some common error codes indicate:
Error Code | Potential Issue |
---|---|
P-Series (P1, P2-P9) | Power Supply Issues |
E-Series (E6-E7, E0-E3) | Communication Failures, Sensor Problems |
U-Series (U4) | System Configuration Issues |
For a complete list of error codes and their meanings, visit our detailed guide on mitsubishi heat pump error codes.
The Role of LED Displays
The LED displays on both the indoor and outdoor units of your Mitsubishi mini split system play a crucial role in error code diagnostics. These displays provide a visual representation of the problem at hand. For example, an E6 error code may flash on the indoor unit’s display, prompting you to check the corresponding issue on the outdoor controller board for more details (212 HVAC).
It’s important to note that while the LED display can guide you to the nature of the problem, some issues, like a tripped molded case circuit breaker, require careful inspection of equipment insulation before attempting to reset (212 HVAC). This precaution helps prevent further damage to the equipment.
Understanding the error codes displayed by your Mitsubishi ductless mini split is the first step in resolving issues. When faced with complex error codes such as mitsubishi ductless mini split e6 error code, mitsubishi ductless mini split p8 error code, or mitsubishi ductless mini split e1 error code, it’s essential to refer to specific guides or seek professional help to ensure accurate and safe troubleshooting.
Common Error Codes Explained
Navigating through the world of your HVAC system can be tricky, especially when it comes to understanding the error codes displayed by your Mitsubishi ductless mini split. The error codes are there to help you pinpoint the issue, so you can determine if it’s something you can handle or if professional assistance is needed. Let’s break down some common error codes related to power supply issues, communication failures, and sensor problems.
Power Supply Issues
When your mini split encounters power supply problems, it’s likely to display specific error codes that indicate the nature of the issue. Here are some common power-related error codes you might encounter:
- Error Code E0: This code suggests there has been a power supply error, potentially due to a power outage or a surge. Check your circuit breaker, and ensure the unit is properly plugged in.
- Error Code E8: Indicates an abnormality with the input current or main circuit voltage. It’s essential to ensure your unit is receiving the correct voltage.
- Error Code P8: Refers to an issue with the outdoor unit fan motor, often related to power supply fluctuations. More on P8 error code.
For a more comprehensive list of power supply-related error codes, refer to our common error codes for Mitsubishi heat pumps.
Communication Failures
Communication errors between the indoor and outdoor units of your ductless mini split can cause the system to malfunction. Here’s what some of these codes represent:
- Error Code E6: This code indicates a signal transmission error. It’s a sign that the indoor and outdoor units are not communicating effectively, which could be due to a wiring issue or a malfunctioning circuit board. Explore the E6 error code in detail.
- Error Code 2502: Points to an outdoor unit communication error. Possible causes include a defective communication cable, a faulty PCB, or incorrect wiring. Troubleshooting steps for error code 2502.
Understanding these error codes is key to troubleshooting Mitsubishi ductless mini split error codes effectively.
Sensor Problems
Sensors play a crucial role in the operation of your mini split system by monitoring temperatures and pressures. Here are some sensor-related error codes:
- Error Code P4: Pertains to a problem with the discharge pipe temperature sensor, which may require sensor replacement or a check on the wiring connections. Further information on P4 error code.
- Error Code E9: Relates to a complication with the outdoor compressor temperature sensor. It may indicate a faulty sensor or issues within the compressor itself. Learn more about the E9 error code.
- Error Code 5611: Signifies an issue with the high-pressure sensor in the refrigerant system. This could signal an overcharge of refrigerant, a leak, or a defective sensor. Addressing error code 5611.
Sensor issues can be complex, and while some may be resolved through a reset, others may require professional intervention. For a detailed guide on sensor problems, visit our section on mitsubishi ductless mini split error codes.
By understanding these common error codes, you can take the first steps in diagnosing problems with your Mitsubishi ductless mini split system. However, if you’re unsure about the issue or the error persists after your troubleshooting attempts, it’s wise to seek help from a qualified technician.
Detailed Error Code Analysis
When your Mitsubishi ductless mini split system encounters an issue, it communicates the problem through specific error codes. These alphanumeric codes can guide you through the troubleshooting process. Here, we’ll delve into the P-Series, E-Series, and U-Series codes, which are commonly displayed when your mini split needs attention.
Troubleshooting P-Series Codes
P-Series codes typically indicate problems related to the performance of the mini split system. For instance:
- P1: This error points to an overvoltage or undervoltage issue and requires checking the power supply for stability.
- P4: Signifies an issue with the discharge pipe temperature sensor, suggesting that the sensor may need to be inspected or replaced (Mitsubishi Electric Malaysia).
- P8: Refers to a malfunction related to the indoor unit’s heat exchanger temperature. It’s advisable to clean the exchanger or check for blockages.
For more detailed information on P-Series error codes, such as the mitsubishi ductless mini split p8 error code, you can refer to the specific articles linked.
Addressing E-Series Codes
E-Series codes are more varied and can indicate a range of issues from power supply problems to sensor malfunctions:
- E0: Implies a power supply problem, and it’s recommended to check the voltage and electrical connections (Mitsubishi Tech Info).
- E6: Indicates a signal transmission error between the indoor and outdoor units, often requiring a check of the wiring and connections (Mitsubishi Electric Malaysia).
- E9: Related to issues with the outdoor compressor temperature sensor, potentially signaling the need for sensor inspection or replacement.
A complete guide to E-Series codes can be found on the mitsubishi ductless mini split error codes page.
Interpreting U-Series Codes
U-Series codes generally point to communication issues between the indoor and outdoor units:
- U4: This error code suggests a communication failure between the units. Inspecting the wiring and connections is crucial.
- U2: Indicates a power supply abnormality. Verifying the voltage and inspecting the PCB (printed circuit board) for damage is recommended.
- U6: Refers to a problem with the outdoor unit’s fan motor, possibly a malfunction or electrical issue.
For each of these codes, it’s important to refer to the technical manual or seek professional assistance if the troubleshooting steps are beyond your comfort level. More about U-Series codes can be found on the common error codes for mitsubishi heat pumps page.
In summary, each series of error codes requires a unique approach to troubleshooting. By understanding what each code represents, you can take the appropriate steps to address the issue. However, when in doubt, especially with complex codes like mitsubishi ductless mini split e9 error code or mitsubishi ductless mini split u4 error code, seeking professional assistance is the best course of action. Regular maintenance can prevent many of these issues from arising, ensuring your system operates smoothly year-round.
When to Seek Professional Help
As a homeowner, you can often troubleshoot and resolve minor issues with your Mitsubishi ductless mini split system by understanding the common error codes for Mitsubishi heat pumps. However, there are times when it’s best to seek professional help, especially when faced with complex issues.
Identifying Complex Issues
Certain error codes and system behaviors can indicate problems that are beyond the scope of DIY fixes. Here are signs that it’s time to call in the experts:
- If your system displays recurring error codes after you’ve attempted to reset or troubleshoot it.
- When you observe unusual noises, smells, or leaks that accompany the error codes.
- If the error code points to an issue with the electrical components of the system, such as a phase loss or phase imbalance, as is the case with error code 6607.
- When the system shuts down completely or fails to respond to the remote control or manual controls.
These complex issues might stem from a deeper, underlying problem that requires a professional assessment to diagnose and resolve, ensuring your system’s longevity and efficiency.
Contacting Technical Support
When you encounter signs of complex issues, reaching out to Mitsubishi Electric’s technical support team is a wise next step. Their team is staffed with experienced engineers who can provide you with troubleshooting guidance, operation advice, and parts recommendations.
For issues that cannot be resolved over the phone or remotely, engaging an authorized service center or a certified technician is crucial. These professionals have the expertise to accurately diagnose and fix errors, ensuring that your system operates at its best.
It is always recommended to have a professional conduct repairs on your system to avoid further damage or voiding any existing warranties. You can find a list of authorized service centers and contact information on the manufacturer’s website. Additionally, Mitsubishi Electric Trane HVAC US offers comprehensive support and service, with a dedicated Project Quality group for world-class assistance (Mitsubishi Comfort).
In conclusion, while some troubleshooting can be done on your own using resources such as mitsubishi ductless mini split error codes, there are situations where professional help is not just beneficial, but necessary. It’s important to recognize when to step back and allow the experts to handle the complexities of your system to ensure safety and proper functionality.
Preventative Measures
Preventative measures are essential in maintaining the health and efficiency of your Mitsubishi ductless mini split system. By taking proactive steps, you can avoid the inconvenience of unexpected breakdowns and the appearance of various error codes.
Importance of Regular Maintenance
Regular maintenance is crucial for keeping your ductless mini split system in top condition. It ensures optimal performance and can prevent the occurrence of common issues that lead to error codes. Here’s what you should keep in mind:
- System Cleaning: Dust and debris can accumulate on your unit’s filters, coils, and other components, which can impact efficiency and air quality. Clean or replace filters regularly, and ensure outdoor units are clear of foliage and debris.
- Inspection: Conduct periodic inspections to check for any signs of wear or damage. Pay attention to unusual noises, smells, or changes in performance, as these can be early indicators of potential problems.
- Professional Check-Ups: Schedule professional maintenance at least once a year. Technicians will perform a thorough check, including inspecting refrigerant levels, testing electrical connections, and ensuring all parts are functioning correctly. This can help catch issues early and prevent future error codes (Mitsubishi Tech Info).
Resetting Your System
Sometimes, your Mitsubishi ductless mini split may simply need a reset to clear an error code. Before resetting, make sure to:
- Check Insulation: Ensure there are no insulation issues with your equipment. Resetting circuit breakers without checking for insulation problems can lead to equipment damage.
- Follow Steps: To reset your system, turn off the unit at the circuit breaker, wait a few minutes, and then turn it back on. This can help clear minor glitches and restore normal operation.
- Be Cautious: If the same error code appears after a reset, it could indicate a more serious issue that requires professional attention.
It’s important to understand that while resetting can be a quick fix, it’s not a cure-all solution. If error codes persist, they should be addressed promptly to avoid escalation of problems (Mitsubishi Electric Malaysia). For more detailed troubleshooting, explore specific error codes like E6, P8, E1, E9, E0, and U4.
By adhering to a consistent maintenance routine and knowing how to properly reset your system when necessary, you can significantly reduce the likelihood of facing disruptive error codes and maintain the longevity and efficiency of your Mitsubishi ductless mini split system.
Additional Resources
When you’re faced with the task of troubleshooting Mitsubishi ductless mini split error codes, having access to the right resources can make a world of difference. From online tools to comprehensive technical manuals, there are various aids available to help you diagnose and address issues with your mini split system.
Utilizing Online Tools
A valuable resource at your disposal is the Mitsubishi Electric Error Code Search Tool, which can offer insights into the cause of a malfunction by simply entering the error code. This tool is designed to provide you with a clear understanding of what each error code signifies and the current status of your air conditioning unit (212 HVAC).
For example, if your system displays codes like UF, UP, or U6, this indicates specific problems that the unit is encountering. The search tool can offer you a starting point for troubleshooting these issues (TK AirPower).
For more detailed error code assistance, such as understanding mitsubishi ductless mini split e6 error code or mitsubishi ductless mini split p8 error code, the error code search tool can be an invaluable guide.
Accessing Technical Manuals
Technical manuals are another critical resource when dealing with error codes. These manuals offer comprehensive information, including step-by-step troubleshooting guides for each error code. For instance, error code 2502 indicates an outdoor unit communication error, which could stem from issues such as a malfunctioning communication cable, a defective PCB, or incorrect wiring.
Mitsubishi ductless mini-split systems come equipped with self-diagnostic functions, and the corresponding service manuals detail how to interpret these diagnostics. The LED lights on the indoor unit will display specific error codes, indicating various issues ranging from power supply problems to sensor malfunctions. It’s recommended that homeowners consult the service manual for the most effective resolution to these errors.
For a comprehensive list of error codes and their meanings, you can refer to our pages on common error codes for Mitsubishi heat pumps, which include issues like the mitsubishi ductless mini split e1 error code, mitsubishi ductless mini split e9 error code, and mitsubishi ductless mini split e0 error code.
In summary, when you encounter error codes on your Mitsubishi ductless mini split system, utilize online tools and technical manuals to guide your troubleshooting process. These resources provide valuable information that can help you quickly identify and resolve issues, ensuring that your mini split system runs efficiently and effectively.
CONTACT US TODAY

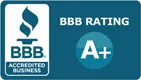

As Seen & Heard On
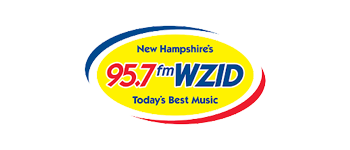
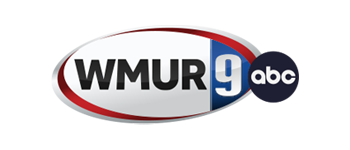

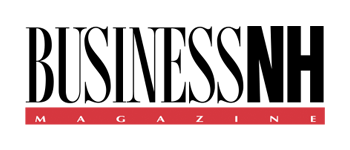
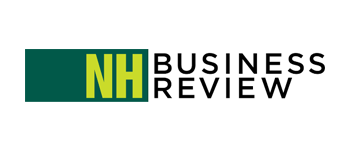
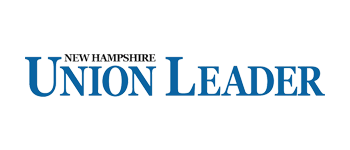
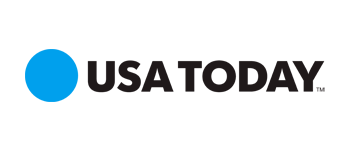
Reach Out to Our Team for More Details
Feel free to call Sanford Temperature Control or fill out the online form for more information. You may also get in touch with our team to schedule an appointment. We look forward to hearing from you.