Conquer the E1 Error: Troubleshooting Mitsubishi Ductless Mini Split
Home >
Understanding the E1 Error Code
When your Mitsubishi ductless mini split system displays an E1 error code, it’s signaling a communication issue that needs your attention. Here’s how you can identify this problem and understand its common causes.
Identifying the E1 Issue
The E1 error code on your Mitsubishi ductless mini split system signifies a disruption in communication between the indoor and outdoor units. This fault can affect various types of units, including wall-mounted, duct-connected, and ceiling-mounted models, to name a few. When this error code appears, the system is typically unable to function properly until the issue is resolved.
It is crucial to accurately identify the E1 error as it can have implications on your system’s performance and longevity. The error may manifest through the system’s inability to cool or heat effectively, or it might shut down altogether. For a comprehensive list of mitsubishi heat pump error codes, including the E1, you can refer to our detailed guides.
Causes of Communication Errors
Communication errors leading to the E1 code can stem from a few different sources:
-
Wiring Issues: Faulty or incorrect wiring between the indoor and outdoor units can lead to communication failures. This is often the primary cause of an E1 error and can be due to loose connections, damaged wires, or improper installation.
-
Faulty Control Boards: The control boards within the indoor or outdoor units are central to operation. If either board has a defect or suffers damage, it can interrupt the communication flow, triggering the E1 error.
-
High Voltage Problems: A less common but possible cause of the E1 error is a high voltage issue, which can lead to the outdoor unit shutting down to prevent damage.
-
Refrigerant Leaks: In rare cases, refrigerant leaks may be responsible for the E1 error. While a leak does not directly cause communication errors, the resulting performance issues can lead the system to generate an E1 code.
If you’re faced with an E1 error code, it’s important to conduct a thorough inspection to determine the root cause. For steps on how to troubleshoot this and other error codes, you can visit our guide on troubleshooting mitsubishi ductless mini split error codes. Understanding these causes will help you address the issue more effectively, whether you choose to tackle it yourself or call in a professional for assistance.
Troubleshooting the Mitsubishi Ductless Mini Split E1 Error Code
Encountering an E1 error code on your Mitsubishi ductless mini split can be challenging, but with the right approach, you can often resolve the issue yourself. The E1 error typically points to a communication glitch between the indoor and outdoor units. Here’s how you can troubleshoot the E1 error code.
Checking Wiring Connections
The first step in troubleshooting the E1 error code is to inspect the wiring connections between your indoor and outdoor units. Loose or damaged wires can disrupt communication, triggering the E1 error. Make sure all connections are secure and there are no signs of wear or damage.
Checkpoint | Action |
---|---|
Terminal connections | Ensure they are tight and not corroded |
Wire insulation | Look for any cracks or wear |
Cable ties | Confirm they are intact and not causing wire pinching |
If you find any issues with the wiring, address them promptly. This might involve tightening loose connections or replacing damaged wires. However, if you’re not comfortable handling electrical components, it might be best to contact a professional.
Inspecting Control Boards
Control boards are the brains of your mini split system, and a malfunction can result in an E1 error. Carefully examine the control boards for any signs of damage, such as burn marks or corrosion. Ensure that all cable connections to the control boards are secure.
In case of visible damage or if the control board has failed, it may need to be replaced. Due to the complexity of the control board and the need for precise diagnosis, you might want to consider seeking assistance from a skilled technician, especially if you’re not familiar with electronic repairs.
Addressing Refrigerant Leaks
A refrigerant leak can lead to a multitude of issues, including the E1 error code. Check for signs of refrigerant leaks, such as oil stains around the refrigerant lines or a hissing sound, which might indicate escaping gas. Refrigerant level checks and repairs should be handled with care due to the potential risks and environmental concerns.
Sign of Leak | Indicator |
---|---|
Oil stains | Possible leak at connections or coils |
Hissing sounds | Gas escaping from a leak |
Ice buildup | Refrigerant lines freezing due to low charge |
If you suspect a refrigerant leak, it’s crucial to get it repaired by a certified professional to ensure the system is recharged correctly and that the leak is properly sealed.
For additional insight into resolving common error codes for Mitsubishi heat pumps, including the E1 error, visit our detailed guide on troubleshooting Mitsubishi ductless mini split error codes. Should you encounter other error codes like E6, P8, E9, E0, or U4, you can refer to our specific articles on Mitsubishi ductless mini split E6 error code, P8, E9, E0, and U4 for further assistance.
When to Call a Professional
While you may be able to perform some basic troubleshooting on your Mitsubishi ductless mini split, there are times when it is best to call a professional. Understanding when to seek out expert assistance can save you time and prevent further issues with your system.
Complexities of DIY Diagnosis
Attempting to diagnose and resolve a ‘mitsubishi ductless mini split e1 error code’ on your own can be challenging. The E1 error code signals a communication error within the system, which can stem from a variety of causes that are not always straightforward to identify. For example, wiring issues, faulty control boards, or refrigerant leaks are complex problems that typically require professional expertise.
Moreover, the process of diagnosing these issues involves navigating the system’s technical manual, which can be quite distinct from other HVAC manufacturers. The manuals provided by Mitsubishi have specific instructions and codes that may not be easily interpreted without proper training (PV Heating, Cooling & Plumbing).
Benefits of Professional Expertise
By consulting a professional HVAC technician, you can ensure that your E1 error is diagnosed and resolved correctly. A qualified technician will not only have the necessary tools and knowledge to address the issue but will also be able to perform the job safely and efficiently.
Professionals bring several key advantages:
- Specialized Training: Mitsubishi factory-endorsed contractors receive special training on the design, installation, and commissioning of Mitsubishi mini-split systems.
- Hands-on Experience: Experienced contractors have hands-on experience with Mitsubishi systems and can draw on this expertise to accurately diagnose and fix your E1 error (PV Heating, Cooling & Plumbing).
- Safety: Certified HVAC professionals know how to handle the complexities of electrical components and refrigerants, ensuring that repairs are done safely.
- Support Network: Expert contractors often have direct connections to the Mitsubishi HVAC design team, providing an additional layer of support and problem-solving if needed.
If your troubleshooting efforts do not resolve the E1 error or if you are unsure about any part of the process, it is recommended to contact a professional. For more information on common error codes and troubleshooting, explore mitsubishi heat pump error codes and consider consulting our comprehensive guides to troubleshooting mitsubishi ductless mini split error codes.
Preventing Future E1 Errors
An E1 error code on your Mitsubishi ductless mini split system signals a communication issue that can be quite a headache to resolve. However, with proper care and attention, you can minimize the chances of this error recurring and ensure your system operates efficiently.
Regular System Maintenance
Regular maintenance is key to preventing the mitsubishi ductless mini split e1 error code. This includes cleaning or replacing air filters, checking refrigerant levels, and inspecting electrical connections for signs of wear or damage. It’s recommended to schedule maintenance at least once a year, ideally before the cooling or heating season begins. Here’s a simple maintenance checklist:
Maintenance Task | Frequency |
---|---|
Clean/Replace Air Filters | Every 1-3 Months |
Check Refrigerant Levels | Annually |
Inspect Electrical Connections | Annually |
Clean Outdoor Unit & Coils | Annually |
By adhering to this schedule, you can ensure that your system remains in top condition and reduce the likelihood of an E1 error. For more detailed information on each of these tasks, refer to the guides on troubleshooting mitsubishi ductless mini split error codes.
Importance of Professional Installation
Proper installation by a certified professional is crucial for the long-term reliability of your Mitsubishi ductless mini split system. Experienced contractors are not only familiar with the unique design and operation of these units but also have access to Mitsubishi’s specialized manuals and support. This expertise is essential for ensuring that your system is installed correctly and functioning at its best.
Choosing a contractor with a strong track record and direct connections to Mitsubishi’s HVAC design team can offer further benefits, such as specialized problem-solving and support.
For peace of mind, always hire a certified HVAC professional for any installation or service needs, especially for complex error codes like E1. Attempting DIY repairs could lead to safety risks or additional damage to your system, so it’s best to rely on professionals who have the training to handle these issues.
In conclusion, regular system maintenance and proper installation by certified professionals are essential practices to prevent future E1 error codes and to keep your Mitsubishi ductless mini split running smoothly. For additional resources on common error codes and their meanings, visit our articles on mitsubishi heat pump error codes and mitsubishi ductless mini split error codes.
Additional Considerations
Maintaining your Mitsubishi ductless mini split system is crucial for its longevity and efficiency. As you navigate the intricacies of the ‘mitsubishi ductless mini split e1 error code’, there are additional considerations to keep in mind, particularly regarding seasonal maintenance and safety during repairs.
Seasonal Maintenance Tips
To ensure your mini split system operates effectively throughout the year, it’s important to follow a few seasonal maintenance guidelines:
-
Spring and Summer: Check the thermostat batteries and reset the circuit breaker as needed. If you notice ice on the coils, this could be a sign that your system is shutting off due to a clogged air filter. Changing the air filter can prevent this issue and improve cooling efficiency.
-
Fall and Winter: The guidelines for servicing your mini split system also apply during colder months. If your system isn’t heating properly, follow the same steps as you would for cooling issues to ensure your unit is serviced efficiently and correctly. This may include checking for blockages or leaks that could affect performance.
For more detailed information on error codes and solutions, explore the mitsubishi ductless mini split error codes page.
Safety During Repairs
When addressing the E1 error code or any other technical issues with your Mitsubishi ductless mini split system, safety should be your top priority:
-
High Voltage Caution: Technicians should exercise extreme caution when testing high voltage components in the outdoor unit to prevent electric shock injuries. Always ensure power to the unit is switched off before beginning any work.
-
Professional Assistance: It’s strongly recommended that troubleshooting and repairs, particularly those relating to the E1 error code, be performed by certified HVAC professionals. This ensures safety and helps prevent potential damage to the system that could occur from incorrect handling (Mitsubishi Tech Info).
Seeking professional expertise can also provide additional benefits, such as warranty preservation and peace of mind. Besides the E1 error code, there are common error codes for mitsubishi heat pumps that you may encounter, including E6, P8, E9, E0, and U4 error codes. Each of these requires specific knowledge and experience to resolve effectively.
For guidance on resolving other error codes, refer to troubleshooting mitsubishi ductless mini split error codes and familiarize yourself with steps to address issues such as the mitsubishi ductless mini split e6 error code or the mitsubishi ductless mini split p8 error code.
Always remember that while some maintenance tasks can be performed by homeowners, such as cleaning filters and ensuring proper airflow, any technical repairs should be left to the professionals to avoid risks and ensure your system remains in optimal condition.
CONTACT US TODAY

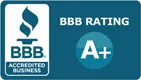

As Seen & Heard On
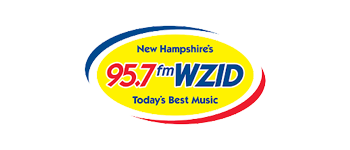
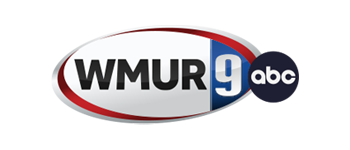

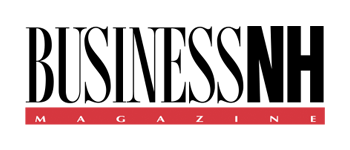
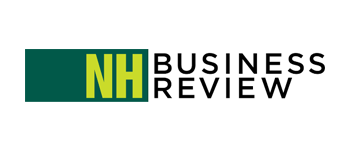
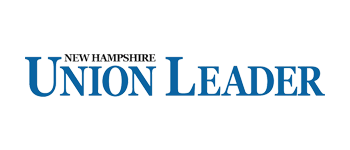
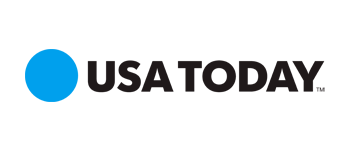
Reach Out to Our Team for More Details
Feel free to call Sanford Temperature Control or fill out the online form for more information. You may also get in touch with our team to schedule an appointment. We look forward to hearing from you.