Demystifying the E6 Error Code: Troubleshooting Mitsubishi Ductless Mini Split
Home >
Understanding the E6 Error Code
When your Mitsubishi ductless mini split system displays an E6 error code, it’s indicating a specific issue that requires your attention. Let’s break down what this error message means and how it affects the operation of your HVAC unit.
Decoding the E6 Message
The E6 error code on a Mitsubishi ductless mini split system typically signifies a communication error between the indoor and outdoor units. This issue may arise from various causes such as wiring defects, control board problems, or faulty sensors, which disrupt the synchrony and data exchange between the two units. Understanding the underlying issue is pivotal for effectively troubleshooting and resolving the problem (JustAnswer).
Symptoms and System Behavior
The manifestation of an E6 error code can be accompanied by your mini split system behaving erratically or failing to function as expected. Symptoms may include:
- The system not turning on or off properly.
- The indoor unit’s fan motor malfunctioning, as reported by GitHub.
- Inconsistent temperatures or lack of response to temperature settings.
- The outdoor unit not communicating effectively with the indoor unit (Reddit).
Recognizing these signs can help you determine that an E6 error code is more than just a random set of characters, but an indicator of a communication problem within your ductless mini split system. For more information on Mitsubishi-specific error codes, you can refer to our comprehensive guide on mitsubishi ductless mini split error codes. If you encounter other error codes such as P8, E1, E9, E0, or U4, visit our pages dedicated to mitsubishi ductless mini split p8 error code, mitsubishi ductless mini split e1 error code, mitsubishi ductless mini split e9 error code, mitsubishi ductless mini split e0 error code, or mitsubishi ductless mini split u4 error code for targeted troubleshooting.
Common Causes of E6 Errors
When your Mitsubishi ductless mini split system presents an E6 error code, it’s essential to understand the common causes behind it. This error typically signifies a communication problem between the indoor and outdoor units, which can stem from a variety of issues.
Communication Breakdown
A communication breakdown is the primary culprit for an E6 error code. This malfunction indicates that the indoor unit is not receiving the correct signals from the outdoor unit. It can be due to several reasons, such as wiring defects, loose connections, or damaged wiring between the two units. It’s crucial to inspect the communication wires for any signs of damage or disconnection.
To diagnose and resolve this issue, refer to our guide on troubleshooting Mitsubishi ductless mini split error codes.
Control Board Issues
Another common cause for the E6 error involves faults within the control board. The error may indicate issues related to the voltage or communication lines that are integral to the operation of the system’s main PCB board. If the control board has defects or has been damaged, it may fail to send or receive the necessary signals to keep the system running smoothly.
If you suspect a control board issue, it is often best to seek professional assistance. A technician can perform a comprehensive assessment and determine whether the control board requires repair or replacement.
Power Supply Problems
Power supply issues can also trigger an E6 error code. These problems may arise if the voltage levels at the indoor or outdoor units are incorrect or if the line voltage is unstable. The error can manifest if there’s a disruption in the power supply or if the system is receiving the wrong voltage (115/230) (HVAC How To).
To address power supply problems, you may need to inspect the electrical connections and ensure that your mini split system is connected to a stable power source. If you’re not familiar with handling electrical components, it’s recommended to contact a professional who can safely check and correct any power supply issues.
Understanding these common causes of E6 errors can help you take the first steps toward resolving the issue. For more information on error codes and how to approach them, explore our resources on common error codes for Mitsubishi heat pumps. If the problem persists, don’t hesitate to consult with a qualified HVAC technician to accurately diagnose and fix your Mitsubishi ductless mini split system.
Diagnosing and Troubleshooting
When your Mitsubishi ductless mini split displays the dreaded E6 error code, it indicates a communication problem between the indoor and outdoor units. This can be a frustrating issue, but with careful diagnostics, you can often pinpoint the problem.
Inspecting Wiring and Connections
The first step in troubleshooting the mitsubishi ductless mini split e6 error code is to inspect the wiring and connections between the indoor and outdoor units. According to JustAnswer, improper wiring or bad connections can cause this error code to appear.
Start by ensuring that all connections are secure and that there are no visible signs of damage or wear on the wires. Check both high voltage and low voltage lines as inconsistencies here are common culprits (HVAC How To).
Connection Type | Things to Check |
---|---|
High Voltage | Ensure voltage at both units is correct (115/230V) |
Low Voltage | Check for secure connections and undamaged wires |
Communication Wires | Inspect for cuts, frays, or loose connections |
If you discover any issues with the wiring, it’s important to address these before proceeding. In some cases, simply resecuring a loose wire can clear the error code.
Checking the Control Board
If the wiring checks out, the next step is to examine the control board. The control board is the brain of your mini split, and issues here can disrupt the entire system. Look for signs of burns, damage, or corrosion, which could indicate that it’s time for a replacement (HVAC How To).
When inspecting the control board, be sure to turn off the power to your mini split to avoid any electrical hazards. If you’re not comfortable performing this step, it may be best to consult a professional.
Testing Sensors and Motors
Finally, the E6 error can sometimes be related to faulty sensors or motors. These components are essential for the proper operation of your mini split, and malfunctions here can disrupt communication between the indoor and outdoor units.
Using a multimeter, you can test the sensors and motors for continuity and proper resistance levels. Refer to your mini split’s manual for the correct specifications. If any components are not functioning within the specified range, they may need to be replaced.
Component | Test |
---|---|
Sensors | Check for continuity and resistance |
Motors | Ensure they are running and not overheated |
Troubleshooting the E6 error code can be complex, and while these steps may help you identify the problem, resolving it can often require expertise. If you’re unsure about any step or if the issue persists, consider calling a professional technician for help. Learn more about when to seek assistance in our guide on troubleshooting mitsubishi ductless mini split error codes.
Remember, it’s important to regularly maintain your mini split to prevent issues like the E6 error code from arising. Regular maintenance not only helps in keeping your unit running smoothly but also in catching potential problems early on. For a comprehensive list of common error codes and their meanings, check out our article on common error codes for mitsubishi heat pumps.
Professional Solutions
When faced with a ‘mitsubishi ductless mini split e6 error code’, sometimes the troubleshooting steps you can perform at home are not enough. In such cases, it’s essential to know when to call in a professional and what to expect during the repair process.
When to Call a Technician
You should consider contacting a professional HVAC technician if:
- The E6 error persists even after you have checked all the connections and components.
- You are not comfortable performing the troubleshooting steps or lack the necessary tools.
- You have performed a reset, and the error code reappears.
- The system’s performance is degrading, and it no longer cools or heats effectively.
Consulting a professional is recommended to ensure that your system is correctly diagnosed and repaired, which can help prevent further damage (JustAnswer). A certified technician will have the expertise and the appropriate diagnostic tools to identify the root cause of the E6 error and resolve it efficiently (TK Air Power).
What to Expect During Repair
When a technician arrives to address the ‘mitsubishi ductless mini split e6 error code’, you can expect them to:
- Conduct a thorough inspection of the system, including all wiring and electrical connections between the indoor and outdoor units.
- Use specialized diagnostic tools to test the functionality of sensors, motors, and control boards.
- Assess the condition of the control board for any visible faults or damage.
- Verify that the power supply to the unit is stable and within the required specifications.
- Provide a detailed explanation of the issue and discuss the necessary repairs or replacement parts.
The technician will also check for any other potential error codes that could be related to the E6 error, such as mitsubishi ductless mini split p8 error code or mitsubishi ductless mini split e1 error code, to ensure a comprehensive solution to the problem.
During the repair process, the technician may discover that one of the control boards is the culprit. In this case, a replacement may be necessary (HVAC How To). The cost and time required for the repair will depend on the extent of the issue and the availability of replacement parts.
By understanding when to call a technician and what to expect during repair, you can ensure that your Mitsubishi ductless mini split system is restored to its optimal operating condition in a timely and professional manner. Remember, addressing the E6 error promptly is crucial for the efficient operation of your system and to prevent further issues. For more information on common error codes for Mitsubishi heat pumps and how to troubleshoot them, visit mitsubishi heat pump error codes and troubleshooting mitsubishi ductless mini split error codes.
Preventing Future E6 Errors
To ensure your Mitsubishi ductless mini split system operates reliably, it’s important to take proactive steps to prevent issues like the E6 error code. Regular maintenance and professional servicing are key strategies.
Regular Maintenance Tips
Regular maintenance is crucial for the longevity and efficiency of your mini split system. Here are some maintenance tasks you can perform:
- Clean or Replace Air Filters: Dirty air filters can restrict airflow, causing the system to work harder. Clean or replace them every month.
- Inspect Wiring and Connections: Periodically check for any loose or damaged wires, as these can lead to communication errors.
- Clean Indoor and Outdoor Units: Dust and debris accumulation can affect the system’s performance. Gently clean the exterior of both units.
- Check for Obstructions: Ensure there is no blockage around the outdoor unit that might restrict air intake or exhaust.
- Review the Manual: Familiarize yourself with the system’s maintenance schedule and follow the manufacturer’s recommendations.
By adhering to these maintenance tips, you can help prevent communication malfunctions and other issues that trigger E6 and other mitsubishi heat pump error codes.
Importance of Professional Servicing
While regular homeowner maintenance is beneficial, professional servicing is essential for more complex tasks and to ensure your system runs optimally. Here are reasons to consider professional servicing:
- Expertise: Technicians have the knowledge and experience to diagnose and fix issues that are not apparent to the untrained eye.
- Equipment Inspection: Professionals use specialized tools to check electrical components, refrigerant levels, and other system aspects that require technical skill.
- Warranty Compliance: Regular professional servicing may be required to keep your system’s warranty valid.
- Safety: Handling electrical components and refrigerants should be done by trained professionals to avoid accidents.
Professional servicing is recommended at least once a year, or as specified by your system’s manufacturer. This maintenance helps prevent common issues such as the E6 error code, which typically indicates a communication breakdown between indoor and outdoor units (TK Airpower).
By combining these regular maintenance tips with the expertise offered through professional servicing, you can help ensure that your Mitsubishi ductless mini split system avoids the dreaded E6 error and continues to function efficiently for years to come. If you’re dealing with other common error codes, such as mitsubishi ductless mini split e1 error code or mitsubishi ductless mini split u4 error code, consulting with professionals can provide you with the necessary troubleshooting steps or repairs.
Resetting Your Mini Split
When your Mitsubishi ductless mini split displays the dreaded E6 error code, indicating a communication error between the indoor and outdoor units, it can be both frustrating and confusing. Fortunately, in some cases, you may be able to clear the error code with a simple reset.
Steps to Clear the E6 Code
To reset the E6 error code on your mini split system, you can follow these steps:
- Power down the unit using the remote or the main power button on the indoor unit.
- Turn off the power at the circuit breaker or the disconnect switch for the mini split system. This ensures that the system is completely without power.
- Wait for approximately 5 minutes. This waiting period allows the system to fully discharge and reset.
- Restore power to the system by turning the breaker or disconnect switch back on.
- Power up the mini split using the remote or the power button on the indoor unit.
After completing these steps, the system should reset and begin operating normally. If the E6 error code clears, no further action may be needed. However, if the error code reappears or persists, further troubleshooting will be necessary to identify and solve the underlying issue. For more information, visit troubleshooting mitsubishi ductless mini split error codes.
When a Reset Isn’t Enough
If the E6 error code does not clear following a reset, it’s a sign that there are deeper issues within your mini split system. Common problems associated with the E6 code include wiring issues, faulty control boards, or power supply problems. These issues may require a more in-depth approach, including:
- Inspecting and ensuring all wiring connections are secure and undamaged.
- Checking the control board for signs of damage or failure.
- Testing sensors and motors to verify their proper function.
- Evaluating the power supply to ensure it’s delivering consistent, adequate voltage.
In these cases, it’s advisable to seek the expertise of a professional technician who can diagnose and repair your system effectively. Professional servicing is crucial, as attempting to fix these issues yourself can lead to further damage or void your warranty. If you’re experiencing the E6 error code or other common error codes for mitsubishi heat pumps, it’s best to call a technician for support.
Remember, while a reset may temporarily clear the E6 error code, it’s not a cure-all for underlying problems. If you’re frequently encountering this or other errors like the mitsubishi ductless mini split p8 error code or the mitsubishi ductless mini split e1 error code, professional help is your best course of action to ensure the longevity and efficiency of your system.
CONTACT US TODAY

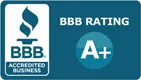

As Seen & Heard On
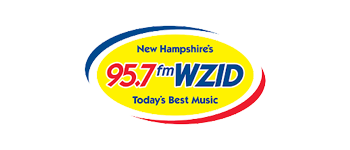
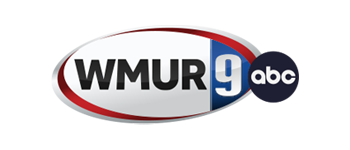

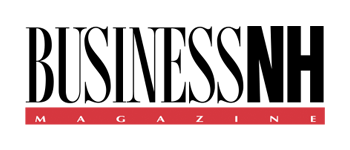
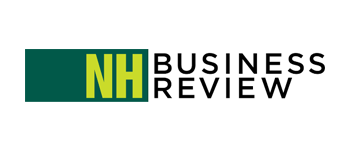
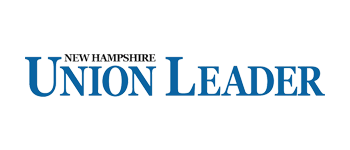
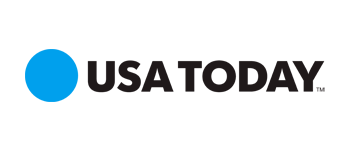
Reach Out to Our Team for More Details
Feel free to call Sanford Temperature Control or fill out the online form for more information. You may also get in touch with our team to schedule an appointment. We look forward to hearing from you.