Unlocking the Solution: Troubleshooting Mitsubishi Mini Split E0 Error
Home >
Understanding Your Mini Split
Introduction to Ductless Systems
Ductless mini splits are a versatile and efficient solution for heating and cooling individual rooms in your home without the need for extensive ductwork. These systems consist of an outdoor unit, which houses the compressor and condenser, and one or more indoor units that deliver conditioned air directly into the living space. The indoor and outdoor components are connected by a set of electrical wires and refrigerant tubing, making installation generally less invasive than traditional HVAC systems.
Common Mitsubishi Error Codes
Mitsubishi ductless mini splits are equipped with a sophisticated diagnostics system that uses error codes to indicate specific issues within the unit. When your mini split encounters a problem, it will display an error code on the indoor unit, the remote controller, or the LED display of the outdoor controller board. These codes are essential for identifying what kind of malfunction has occurred, allowing you to take the appropriate steps to resolve the issue.
A few standard error codes you might encounter include:
- E0: Generally indicates “No Fault” or a potential communication issue between the indoor and outdoor units. PIONEER Mini Split
- E6: Suggests a communication error in the system. mitsubishi ductless mini split e6 error code
- P8: Points to an issue with the temperature sensors. mitsubishi ductless mini split p8 error code
- E1, E2: Signal other specific system errors that require diagnosis. mitsubishi ductless mini split error codes
Here is a table summarizing some of the common error codes for Mitsubishi heat pumps:
Error Code | Possible Cause |
---|---|
E0 | No Fault/Communication Issue |
E6 | Communication Error |
P8 | Temperature Sensor Issue |
E1 | System Error |
E2 | System Error |
Understanding these error codes is the first step in troubleshooting your Mitsubishi ductless mini split. For a more comprehensive list of Mitsubishi error codes and their meanings, you can refer to our article on common error codes for Mitsubishi heat pumps. If you encounter an error code not listed here, such as E9, U4, or E1, please see our specific articles on mitsubishi ductless mini split e9 error code, mitsubishi ductless mini split u4 error code, and mitsubishi ductless mini split e1 error code for targeted troubleshooting advice.
Decoding the E0 Error Code
Understanding the E0 error code on your Mitsubishi ductless mini split system is essential for proper diagnosis and ensuring your unit functions optimally. Let’s break down what this code signifies and the potential causes behind it.
What Does E0 Mean?
The E0 error code on a Mitsubishi ductless mini split generally suggests “No Fault,” which implies that the unit has not detected any specific errors and should be operating correctly (PIONEER Mini Split). This code may appear when the unit is initially powered on or during its regular functioning. However, if you’re seeing this code and your unit is not operating as expected, it may indicate a communication issue.
Causes of the E0 Code
While the E0 code could mean there are no issues with your system, it may also point to a communication problem between the indoor and outdoor units. This could stem from various factors:
-
Incorrect Wiring: Proper connections between the indoor and outdoor units are crucial for communication. Errors in the wiring could disrupt the signal exchange, causing the E0 error to display.
-
Interference: External factors such as electrical interference can affect the communication between the units.
-
Faulty Components: If certain components within the indoor unit, such as the EEPROM chip, are not functioning correctly, the E0 error may be triggered. The EEPROM chip functions as the “brain” of the indoor unit, holding critical data and configurations. Issues with this chip can arise due to several reasons:
-
Power surges that overwhelm the system
-
Main control board failures
-
Improper initial installation
These issues can lead to the corruption of the EEPROM chip, prompting the E0 error code (Mitsubishi Electric UK).
- Resetting the Unit: As a first step in troubleshooting, you may attempt to reset the unit by switching it off at the circuit breaker for at least one minute before turning it back on. If the E0 error persists after this reset, it’s a sign that further investigation is needed.
If you continue to experience issues after performing initial checks, it might be time to seek professional help. For more guidance on troubleshooting Mitsubishi ductless mini split error codes, visit our comprehensive guide on troubleshooting mitsubishi ductless mini split error codes. It’s important to address error codes promptly to prevent more significant issues down the line and to maintain the longevity and efficiency of your HVAC system. For more detailed information on common error codes and when to contact a technician, explore our sections on common error codes for mitsubishi heat pumps and other specific error codes like mitsubishi ductless mini split e6 error code or mitsubishi ductless mini split p8 error code.
Troubleshooting the E0 Code
Encountering an E0 error code on your Mitsubishi ductless mini split can be puzzling since it typically signifies “No Fault” or that no error has been detected by the unit (PIONEER Mini Split). However, if your system isn’t functioning correctly and still displays this code, it’s crucial to perform some initial checks and resets.
Initial Checks and Resets
Firstly, ensure that your mini split is indeed displaying an E0 error, as this code is often misunderstood due to its “No Fault” indication. If confirmed, the issue likely lies in the communication between the indoor and outdoor units, which could stem from incorrect wiring, interference, or a malfunctioning component (PIONEER Mini Split).
Here are some initial steps you can take to address an E0 error code:
- Power Cycle the Unit: Turn off the mini split at the circuit breaker, wait for at least one minute, and then turn it back on. This reset can often clear transient faults and restore normal operation.
- Check the Wiring: Inspect all electrical connections between the indoor and outdoor units to ensure they are secure and free of damage. Look for any signs of wear, loose connections, or corrosion.
- Inspect for Interference: Ensure there are no external sources of electrical interference near the communication wires that could disrupt the signal between units.
- EEPROM Chip: Consider the possibility of a corrupted EEPROM chip on the indoor unit, which may occur due to power surges or board failures (Mitsubishi Electric UK).
When to Seek Professional Help
If the initial checks and reset do not resolve the E0 error code, it’s time to seek professional assistance. Here are scenarios where you should contact a technician:
- Persistent Error: If the error code reappears after resetting the unit, this indicates a deeper issue that requires expert diagnosis.
- Faulty Components: Replacement of the main control board or EEPROM chip is not a DIY task and requires the expertise of a certified technician (Mitsubishi Electric UK).
- Complex Diagnostics: An HVAC professional can run comprehensive diagnostics to pinpoint the exact cause of the communication failure.
Remember, attempting to fix complex electrical components on your own can be dangerous and may void your warranty. It’s always safer and more effective to rely on skilled technicians who have experience troubleshooting Mitsubishi ductless mini split error codes.
As you navigate the process of addressing the E0 code, keep in mind that regular maintenance can prevent many common issues. Familiarize yourself with other mitsubishi heat pump error codes to better understand your system and know when professional intervention is needed.
Preventing Future Errors
Maintaining your Mitsubishi mini split system is not only about fixing issues as they arise but also about preventing future problems. Regular care and attention can save you from inconvenient breakdowns and costly repairs.
Importance of Regular Maintenance
Regular maintenance is essential for keeping your Mitsubishi mini split system running smoothly. By performing routine checks and cleanings, you can minimize issues, maximize efficiency, and extend the operational lifespan of your system. Maintenance tasks include:
- Cleaning or replacing filters every month to ensure clean airflow
- Checking thermostat settings to make sure they are accurate
- Clearing blocked vents and ensuring there is no furniture or drapes blocking them
These simple steps can have a significant impact on the performance and longevity of your mini split system. Set reminders for yourself to perform these tasks, or consider setting up a maintenance schedule with a professional service technician for peace of mind. For more detailed guidance on upkeep, explore our comprehensive guide on troubleshooting mitsubishi ductless mini split error codes.
Recognizing Signs of Trouble
It’s equally important to be aware of early warning signs that might indicate potential issues with your mini split system. Being proactive when you notice anything amiss can help you avoid the dreaded E0 error code and other such complications. Here are signs to watch for:
- Unusual noises during operation
- Decreased heating or cooling efficiency
- Unexpected increases in energy bills
- Frequent cycling on and off
- The emergence of musty or odd smells
If you begin to notice any of these symptoms, it might be time to delve further into potential causes. While many minor problems can be addressed through routine troubleshooting, more complex repairs or decoding complicated issues may necessitate professional support. Consult with certified Mitsubishi installers and service technicians for swift restoration of your comfort system. For information on other error codes, visit our mitsubishi heat pump error codes page.
Understanding the significance of consistent maintenance and recognizing the early signs of trouble can go a long way in preventing future errors. It empowers you to take timely action, ensuring your Mitsubishi mini split system remains a reliable source of comfort in your home.
Beyond the E0 Code
Your Mitsubishi ductless mini split system is a complex piece of machinery designed to provide you with comfort throughout the seasons. While the E0 error code might be your current focus, it’s just one of many signals the system uses to communicate issues to you.
Other Mitsubishi Error Codes
Mitsubishi systems are equipped with self-diagnostic functions that display various error codes when malfunctions occur. These codes range from E0-E9 and include others like P8, U4, and more. Each code corresponds to a specific issue within your ductless system. For instance, you might encounter:
- E6: An issue related to the indoor/outdoor unit communication (mitsubishi ductless mini split e6 error code)
- P8: Abnormality in the pipe temperature (mitsubishi ductless mini split p8 error code)
- E1: Indoor PCB error (mitsubishi ductless mini split e1 error code)
- E9: Indoor/outdoor unit communication error (mitsubishi ductless mini split e9 error code)
- U4: System communication error (mitsubishi ductless mini split u4 error code)
You can find a comprehensive list of these error codes and their meanings in our guides on mitsubishi heat pump error codes and mitsubishi ductless mini split error codes. Understanding these codes is essential for troubleshooting your system effectively.
When to Contact a Technician
While some error codes can be resolved with basic troubleshooting steps, such as resetting the power or checking for obvious wiring issues, there are instances when it’s best to call in a professional. Here are a few scenarios when you should seek expert assistance:
- When error codes persist after performing basic troubleshooting steps.
- If you notice unusual noises, smells, or performance issues following an error code display.
- In cases where the error code indicates a serious internal issue, such as a PCB error or a system communication error.
- If you are not comfortable performing the troubleshooting steps or if you lack the necessary tools and expertise.
Attempting to fix complex issues without proper knowledge can be dangerous and might lead to further damage to your system. It’s important to consult a certified Mitsubishi technician who can accurately diagnose and fix the problem. For assistance with troubleshooting mitsubishi ductless mini split error codes, our resources are available to guide you.
In summary, while the E0 error code might signal a communication issue or a fault within the indoor unit’s EEPROM chip, it’s just one of many potential error codes your Mitsubishi system can display. For each error code, there’s a specific set of causes and troubleshooting steps. Always remember that seeking professional help for your Mitsubishi ductless mini split system issues is the safest and most reliable way to ensure your system’s longevity and performance.
CONTACT US TODAY

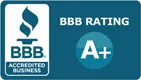

As Seen & Heard On
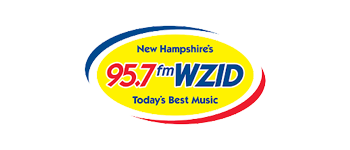
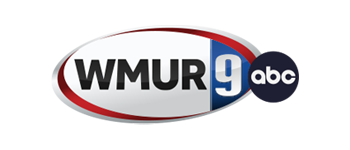

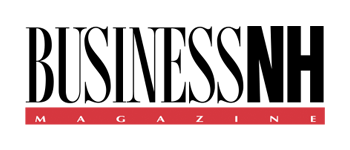
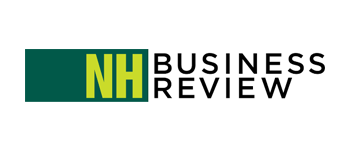
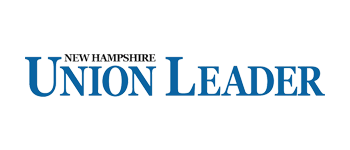
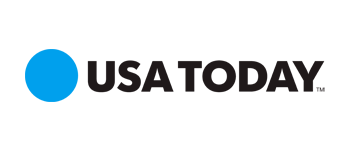
Reach Out to Our Team for More Details
Feel free to call Sanford Temperature Control or fill out the online form for more information. You may also get in touch with our team to schedule an appointment. We look forward to hearing from you.