Troubleshooting Your Boiler: What to Do When Its Not Turning On
Home >
Understanding Boiler Issues
Navigating the complexities of boiler issues can be daunting. Understanding common problems and the significance of regular maintenance is key to keeping your boiler reliable, especially when faced with the dreaded situation of a ‘boiler not turning on’.
Identifying Common Problems
Boilers are intricate systems, and a multitude of issues can lead to them not powering up. These challenges can range from simple fixes to more complex problems requiring professional attention. Here are some common boiler issues you might encounter:
- Lack of power due to tripped circuit breakers or blown fuses (Supertech HVAC)
- Low water pressure, which can be indicated on the boiler’s pressure gauge
- Thermostat malfunctions, such as dead batteries or incorrect temperature settings (Masters Heating & Cooling)
- Air trapped in the system, which can inhibit circulation and heating efficiency
- Complications with the pilot light, such as it not staying lit or failing to ignite (boiler pilot light keeps going out)
- Boiler leaks that could lead to pressure loss and system malfunctions (boiler leaking water)
Understanding these common problems is the first step in troubleshooting your boiler. However, many boiler issues can be preempted by regular maintenance.
Importance of Regular Maintenance
Maintaining your boiler can not only prevent the distress of a cold home when the system fails to start but also save you from the substantial costs associated with repairs or replacements, with average repair costs around $354 (Forbes). Regular maintenance includes:
- Scheduled cleaning and inspections to keep components functioning optimally
- Seasonal servicing to address any potential issues before peak usage times
- Monitoring system pressure to ensure it remains within the recommended range (boiler pressure too high)
By adhering to a maintenance routine, you can extend the life of your boiler, enhance its performance, and decrease the likelihood of facing emergency breakdowns. In instances where your boiler does encounter issues, such as not igniting (boiler not igniting) or producing a gas odor (boiler smells like gas), you will have a clear record of maintenance to help diagnose the problem swiftly.
Engaging in preventive measures and recognizing the need for professional servicing when necessary can lead to a more efficient and reliable boiler system, ensuring your home remains warm and comfortable.
When Your Boiler Won’t Start
Confronting a boiler that won’t activate can be a cause for concern. Here are some steps to diagnose the problem. Remember, if you’re unsure about any procedure, it’s best to consult with an HVAC professional.
Checking Power Sources
Firstly, confirm that your boiler is receiving power. Check your home’s electrical supply and ensure that the fuse dedicated to the boiler hasn’t blown. The absence of power could be a simple reason why your boiler is non-responsive. If you’re not comfortable checking the fuse or if the problem persists, it may be time to contact an HVAC technician. For further details on power-related issues, visit boiler not firing up.
Thermostat Troubleshooting
A faulty thermostat might be the culprit if your boiler remains inactive. Try adjusting the thermostat settings; if there’s no response from the boiler, consider replacing the batteries or recalibrating the device. Thermostat issues are common, and resolving them can be straightforward (Gregor Heating). For a step-by-step guide on thermostat troubleshooting, check out boiler not producing hot water.
Water Pressure Checks
Your boiler’s pressure level is pivotal for its operation. If the pressure is too low, the system’s safety mechanisms may prevent the boiler from starting. Examine the pressure gauge; if it indicates low pressure, you’ll need to adjust it to the correct level. For more information on adjusting water pressure, see boiler pressure too high.
The Pilot Light and Ignition
For boilers with a pilot light, ensure that it’s lit. If it keeps going out or won’t light at all, there might be an issue with the ignition system. Faulty ignition components, such as leads or electrodes, may require cleaning or replacement. Gas supply issues, like a closed valve or lack of gas, could also prevent ignition. For these problems, it may be safer to call a professional, but you can find more information on common ignition issues at boiler pilot light keeps going out and boiler not igniting.
Boiler issues can range from simple fixes to more complex problems that require professional assistance. By following these steps, you may be able to identify the issue and decide on the best course of action. Remember, regular maintenance can often prevent these situations. If you suspect gas-related issues, such as a boiler smells like gas, or if the boiler is overheating, prioritize safety and contact an HVAC technician immediately.
DIY Fixes vs. Professional Help
When faced with a ‘boiler not turning on’ situation, it’s crucial to discern when a simple DIY fix is appropriate and when it’s time to call in a professional HVAC technician. This knowledge not only ensures your safety but can also save you time and money.
Simple Solutions to Try
Before reaching out for expert help, there are a few troubleshooting steps you can attempt:
- Check Power Sources: Verify that your boiler is receiving power. Look for tripped circuit breakers or blown fuses in your electrical panel. A simple reset of a circuit breaker or replacing a fuse might be all that is needed to restore power to your boiler.
- Thermostat Troubleshooting: Ensure that your thermostat has fresh batteries if it is battery-operated and that it is set to ‘Heat’ mode. The temperature setting should be higher than the current room temperature to signal your boiler to turn on. (Supertech HVAC) and (Masters Heating & Cooling)
- Water Pressure Checks: Low water pressure can prevent a boiler from operating. Check the pressure gauge on your boiler and consult your user manual to verify the correct pressure range. If the pressure is too low, you might need to repressurize the system.
- Pilot Light and Ignition: If your boiler has a pilot light, make sure it’s lit. If not, follow the manufacturer’s instructions to relight it safely. For newer boilers with electronic ignition, if the ignition is not working, this may require professional assistance.
If these steps do not resolve the issue or if you are uncomfortable performing them, it’s time to call a professional.
When to Call an HVAC Technician
Even if you’re a hands-on homeowner, certain boiler issues should be handled by professionals due to the complexity and potential safety risks involved. Here are scenarios when you should definitely contact an HVAC technician:
- Persistent Issues: If the boiler repeatedly trips the circuit breaker or if the pilot light keeps going out, this indicates a deeper issue that requires expert diagnosis and repair.
- Gas Supply Problems: If you suspect a problem with the gas supply or smell gas, you should immediately stop trying to fix the issue yourself. Gas leaks are dangerous and require immediate attention from a professional. (boiler smells like gas)
- Error Codes: If your boiler’s control panel is displaying error codes or fault indicators, a technician can accurately interpret these signals and address the underlying problem. (boiler not firing up)
- No Hot Water: If your boiler isn’t producing hot water or is showing signs of overheating, these are symptoms that need professional inspection. (boiler not producing hot water) and (boiler overheating)
Remember, while it’s beneficial to know the basics of troubleshooting, never attempt repairs that are beyond your skill level or that could compromise your safety. Regular maintenance by a certified HVAC technician can prevent many issues, and professional help can ensure that your boiler operates efficiently and safely.
Preventive Measures
Taking proactive steps to maintain your boiler can save you from the stress and discomfort of a chilly home when your heating system decides to take an unexpected break. Here, you’ll learn how to keep your boiler in top shape, potentially preventing the dreaded ‘boiler not turning on’ scenario.
Regular Inspection and Cleaning
A well-maintained boiler is less likely to fail you, especially during the times you need it most. Regular inspection and cleaning are crucial to ensure its proper functioning. By keeping an eye on your boiler, you can identify and solve minor issues before they escalate into major problems.
Here are some inspection and cleaning steps you can take:
- Visually inspect the boiler for any signs of wear, leaks, or corrosion.
- Check the flame of the boiler; it should be a clear blue. A yellow or orange flame could indicate a problem.
- Ensure that all vents and flues are free from obstructions.
- Clean any dust or debris from the boiler’s exterior and the surrounding area to prevent blockages and improve efficiency.
You can find more detailed guidelines on regular boiler maintenance, including steps for boiler leaking water or boiler pressure too high, which could be early signs of issues.
Seasonal Boiler Servicing
Just like your car needs regular servicing to run smoothly, your boiler also benefits from seasonal check-ups. Experts from Boiler Central recommend getting your boiler serviced by a professional HVAC technician at least once a year, preferably before the onset of winter. This can ensure that your system is in good working condition and help address any potential problems that may stop your boiler from turning on when you need it.
During a service visit, a technician will:
- Perform a thorough inspection of the boiler and its components.
- Clean the heat exchanger, burner, and other critical parts.
- Test safety controls and check for any gas or carbon monoxide leaks.
- Assess the boiler’s efficiency and make any necessary adjustments.
By arranging for seasonal servicing, you not only ensure the longevity of your boiler but also its efficiency and safety. If you notice any concerning issues like a boiler pilot light keeps going out or your boiler not igniting, it’s best to seek professional help sooner rather than later.
Remember, preventive maintenance is key to the longevity and reliability of your boiler. Regular inspections and seasonal servicing can help keep your home warm and cozy, preventing unexpected and inconvenient breakdowns. For more tips on keeping your boiler running smoothly and avoiding issues such as boiler keeps shutting off or boiler not producing hot water, check out our comprehensive guides.
Deciphering Boiler Error Codes
When your boiler is not turning on, one of the first things to check is the control panel for any error codes or fault indicators. These codes provide valuable information about the nature of the problem and can guide your troubleshooting efforts.
Recognizing Fault Indicators
Error codes are typically displayed as a series of flashing lights or a specific symbol on your boiler’s control panel. For example, a common fault indicator is a flashing triangle symbol, which points to potential issues such as low water pressure or circulation problems (JustAnswer). Recognizing these symbols is the first step in diagnosing the problem with your boiler.
Here is a quick reference table for some common boiler error codes:
Symbol | Possible Issue |
---|---|
Flashing Triangle | Low water pressure or circulation issue |
Exclamation Mark | Safety cut-off activated |
Snowflake | Frost protection activated |
Flame with a Cross | Ignition failure |
It’s essential to consult your boiler’s manual for a complete list of error codes and their meanings, as symbols and indications can vary between manufacturers and models.
Responding to Control Panel Symbols
Once you’ve identified the fault indicator on the control panel, you can begin to address the underlying issue. Here are a few examples of common symbols and how to respond:
-
Flashing Triangle: Check the boiler’s water pressure gauge. If the pressure is too low, you may need to repressurize the system to get it running again. This symbol may also indicate an issue with the circulation pump, requiring inspection or replacement (JustAnswer).
-
Exclamation Mark: This symbol often signals that the boiler’s safety cut-off has been activated. You may need to reset the boiler, but if the problem persists, seek professional help.
-
Snowflake: If this symbol appears, your boiler’s frost protection has been activated, which typically occurs in cold temperatures to prevent freezing. Ensure that your home’s heating is set to an appropriate level to prevent freezing conditions.
-
Flame with a Cross: This indicates an ignition failure, which could be due to several issues like a faulty ignition system or problems with the gas supply. Check if your other gas appliances are working and reset the boiler. If the problem remains, contact a technician for a detailed inspection.
If after consulting the control panel you are still unsure about the cause of your ‘boiler not turning on’, it may be time to seek assistance. For issues related to boiler not igniting or if your boiler pilot light keeps going out, it’s advisable to call a professional HVAC technician to safely diagnose and repair your boiler.
Remember, while some issues can be resolved with straightforward fixes, others may require in-depth knowledge and expertise. When in doubt, err on the side of caution and consult a professional to avoid risking further damage to your boiler or your home.
Maintenance Tips for Longevity
To ensure that your boiler remains in optimal condition and to minimize the chances of encountering the issue of your boiler not turning on, it’s essential to follow a proper maintenance routine. Here are some fundamental maintenance tips that can extend the life of your boiler and help avoid emergency breakdowns.
Keeping Components Clean
Regular inspection and cleaning are crucial to maintain your boiler’s longevity and prevent emergency breakdowns. Dirt and debris can accumulate in various parts of the boiler system, potentially leading to electrical or mechanical failures. By keeping components clean, you help ensure the proper functioning of your boiler and avoid unexpected shutdowns.
Key areas to focus on include:
- The burners, where dust and debris can accumulate and impede performance.
- The heat exchanger, which should be free of soot for efficient heat transfer.
- The vents and flues, to ensure there are no obstructions that could affect combustion.
Experts from Forbes and Heating Help Forum agree that regular cleaning, inspecting, and testing of these components can significantly prevent issues like your boiler not igniting.
Monitoring System Pressure
Maintaining the correct system pressure is vital for your boiler to operate effectively. Both low and high pressure can lead to performance issues. Regularly check the pressure gauge to ensure that it is within the recommended range (typically between 1 and 2 bar).
If you notice that the pressure is too low, it may be necessary to repressurize the system. Conversely, if the boiler pressure is too high, it could be indicative of other issues, such as a fault in the expansion vessel or a need to bleed your radiators.
Refer to your boiler’s manual for guidance on how to adjust the pressure or consult a professional if you’re unsure about the proper steps to take.
Avoiding Emergency Breakdowns
Proactive measures can significantly reduce the risk of your boiler unexpectedly shutting off. In addition to keeping the components clean and monitoring system pressure, consider the following:
- Schedule regular servicing by a qualified HVAC technician to ensure all parts are in working order.
- Watch for early signs of potential issues, such as strange noises, leaking water, or smells like gas, and address them promptly.
- Familiarize yourself with your boiler’s error codes and troubleshoot accordingly.
- Implement preventative measures such as insulating pipes to prevent freezing during colder months.
By adhering to these maintenance tips, you can significantly extend the lifespan of your boiler, improve its efficiency, and reduce the likelihood of facing the inconvenience of a boiler not producing hot water or other common issues.
Remember, while DIY maintenance can be effective for simple tasks, it’s important to know when to seek professional help, especially when dealing with complex or hazardous problems. Regular professional servicing is a small investment that can help avoid costly repairs and ensure your boiler operates safely and efficiently for years to come.
CONTACT US TODAY

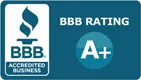

As Seen & Heard On
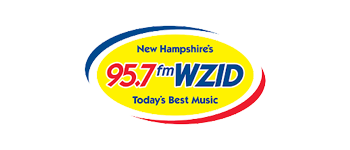
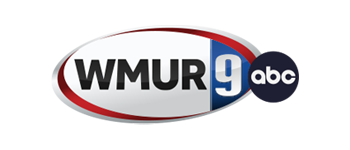

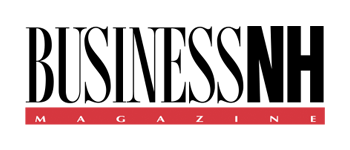
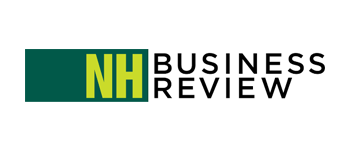
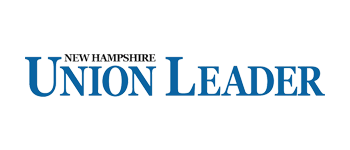
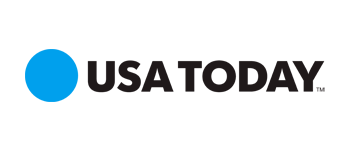
Reach Out to Our Team for More Details
Feel free to call Sanford Temperature Control or fill out the online form for more information. You may also get in touch with our team to schedule an appointment. We look forward to hearing from you.