Empower Your Pump: Resolving the Well Pump Not Turning On
Home >
Understanding Well Pump Issues
When dealing with a well pump not turning on, it’s important to understand the underlying issues that can cause well pump failure. Proper understanding and regular maintenance can help you avoid many common problems.
Maintenance Importance
Regular maintenance is crucial for the smooth operation of your well pump. Pumps require periodic maintenance and servicing to function correctly (JEE Pumps). Neglecting this can lead to serious problems, such as:
- Reduced lifespan
- Increased energy consumption
- Sudden pump failures
Regular inspections can identify parts that are worn out or need replacement. Replacing these components as per the manufacturer’s schedule can prevent unexpected breakdowns. You might want to consider professional inspections to keep your pump in optimal condition.
Maintenance Task | Frequency |
---|---|
Inspect Well Pump | Annually |
Replace Worn Parts | Per Manufacturer’s Schedule |
Professional Inspection | Every 3-5 Years |
Impact of Foreign Objects
Foreign objects getting into your pump system can cause severe damage. Dirt, debris, rocks, or gravel can lead to blockages or damage the internal components of your pump (JEE Pumps). The common results of such blockages include:
- Reduced water flow
- Increased wear and tear
- Potential damage to the piping system
To prevent foreign object intrusion, consider installing protective screens or filters. Regularly check and clean these filters to ensure they are functioning correctly.
Understanding these issues can save you from costly repairs and replacements. Regular maintenance and vigilance can help in keeping your pump in top-notch condition. If you face issues, refer to our troubleshooting well pump problems guide for more detailed steps. For those considering professional help, understanding the cost to replace a well pump might be beneficial.
Common Causes of Well Pump Failure
Understanding the common causes behind a well pump not turning on is crucial for homeowners. This section will cover three major reasons: worn out parts, incorrect installation, and electrical problems.
Worn Out Parts
Well pumps consist of various mechanical components that can wear out over time. Lack of proper maintenance is a significant reason for pump failure. Components like bearings, seals, and impellers can degrade, reducing the efficiency and performance of the pump. Regular inspections and timely replacements are essential to keep your pump functioning properly.
Commonly Worn Out Parts | Average Lifespan (Years) |
---|---|
Bearings | 5-10 |
Seals | 3-5 |
Impellers | 6-10 |
Keeping track of part lifespans can help in scheduling maintenance and avoiding sudden pump failures. If you’re experiencing issues like your well pump keeps running constantly, it’s time to check the condition of these worn parts.
Incorrect Installation
Incorrect installation of a well pump can cause numerous problems and eventually lead to pump failure. It’s crucial to follow the pump manufacturer’s recommendations for proper installation. Misalignment, improper mounting, and inadequate sealing are common installation errors that can affect the pump’s performance and lifespan.
Ensuring that the pump is correctly installed from the outset can save time and money in the long run. If you recently had a new pump installed and it’s not functioning as expected, the root cause might be improper installation. For more detailed guidance, visit our article on how to prime a well pump.
Electrical Problems
Electrical problems such as voltage surges, power outages, or tripped circuit breakers can damage a well pump, leading to failure (JEE Pumps). Protective devices like surge protectors can help safeguard the pump, but sudden electrical surges can still inflict damage.
Common electrical issues include:
- Tripped Circuit Breaker: Resets the electrical connection but should be checked for underlying issues.
- Damaged Wiring: Inspect and replace any faulty wiring.
- Improper Connection: Ensure all connections are secure and correct.
Electrical Issue | Symptom | Solution |
---|---|---|
Tripped Circuit Breaker | No power to pump | Check and reset breaker |
Damaged Wiring | Intermittent power | Inspect and replace wiring |
Improper Connection | No or low water pressure | Secure all connections |
If your well pump fails to turn on due to electrical issues, consult our thorough guide on troubleshooting well pump problems.
Understanding these common causes can help you diagnose issues more effectively and take appropriate action to resolve them. Regular maintenance, correct installation, and monitoring of electrical components are key to keeping your well pump in good working condition. For more information on recognizing issues early, visit our page on signs of well pump failure.
Addressing Well Pump Not Turning On
When your well pump fails to turn on, it can cause significant inconvenience. Identifying the underlying issue is key to resolving the problem. Here are common reasons why a well pump might not turn on and how to address them.
Power Problems
One of the most common reasons for a well pump not turning on is power-related issues. Several power problems can disrupt the functionality of your well pump:
- Tripped Circuit Breaker: Check your home’s circuit breaker panel to see if a breaker has tripped. Resetting the breaker could resolve the issue.
- Damaged Wiring: Inspect the wiring connected to your well pump for any visible signs of damage or wear. Damaged wiring may require professional repair or replacement.
- Improper Pump Connection: Ensure the pump is connected properly to its power source. Loose or improper connections can prevent the pump from operating.
Power Problem | Common Solution |
---|---|
Tripped Circuit Breaker | Reset the breaker |
Damaged Wiring | Repair or replace wiring |
Improper Connection | Verify and secure connections |
For detailed troubleshooting, visit our guide on checking electrical connections.
Water Table Drop
If your well pump is not turning on, it could be due to a drop in the water table. The water table level can fluctuate, especially during dry seasons, which might cause the pump to lose its prime.
- Check Water Levels: Assess the water level in your well. You may need to measure the water level to compare it with the pump’s required operational depth.
- Priming the Pump: If the water level has dropped, you might need to re-prime your well pump. For more information on how to do this, refer to our article on how to prime a well pump.
Symptom | Common Solution |
---|---|
Low Water Level | Measure and compare water levels |
Loss of Prime | Re-prime the well pump |
Inadequate Pump Size
An improperly sized well pump can also lead to functionality issues. If the pump is too small, it may not be able to draw sufficient water to meet your household demands.
- Assess Pump Specifications: Review the specifications of your well pump to ensure it is appropriate for your well’s depth and your household’s water needs.
- Consult Professionals: If you’re unsure, consulting with a professional can help you determine if the pump’s size is adequate. A professional can recommend upgrading to a higher capacity pump if needed.
Issue | Common Solution |
---|---|
Inadequate Pump Size | Review specifications and consult a professional |
For more in-depth guidance, take a look at our article on the appropriate cost to replace well pump and getting the right size for your needs.
Addressing the reasons why your well pump is not turning on often involves checking the power, water table, and pump size. By understanding these elements, you can troubleshoot effectively and restore your water supply. For additional tips, explore our resources on signs of well pump failure and adjusting well pump pressure switch.
Preventive Maintenance Tips
Regular maintenance is essential for preventing your well pump from experiencing issues such as not turning on. Here are some crucial tips to help maintain the efficiency and longevity of your well pump.
Sediment Buildup
Sediment buildup is a common problem that can affect the performance of your well pump. Sediment such as sand, silt, or rust can enter the well, compromising the pump’s efficiency (McCall Brothers Inc.). The accumulation of dirt, small stones, and hard water minerals can degrade pump performance and obstruct water flow.
Indications of sediment buildup include gritty water or decreased water flow from your well pump. If you notice these signs, it may be time to have a professional inspect the system and, if necessary, replace the pump or the well screen affected by contaminants (Blair & Norris). Regular maintenance and cleaning can help prevent sediment buildup, ensuring your well pump operates effectively.
Professional Inspections
Professional inspections are crucial for maintaining the efficiency of your well pump. It is recommended to have your well pump inspected every six months to ensure maximum efficiency (Perry’s Pump Repair). These inspections should include:
- Ohms tests
- Amperage measurements
- Inspection for wiring corrosion
Regularly scheduled inspections by a professional can save energy and prevent future problems. For more information on dealing with potential issues, visit our article on troubleshooting well pump problems.
Inspection Task | Frequency |
---|---|
Ohms Test | Every 6 months |
Amperage Measurements | Every 6 months |
Wiring Corrosion Check | Every 6 months |
Bug Infestations
Bug infestations can significantly impact your well pump’s efficiency. Bugs such as ants can damage the copper wiring in the system, leading to increased electricity bills. Regularly check for bugs, loose wiring, and leaks to prevent these issues (Perry’s Pump Repair).
Preventive measures can include:
- Adding mothballs near the well pump to deter bugs
- Regularly lubricating moving parts to keep the system running smoothly
If you encounter any issues like a malfunctioning pressure switch, you might need to consider replacing well pump pressure switch.
By following these preventive maintenance tips, you can keep your well pump in optimal condition and avoid common issues such as the pump not turning on. Regular maintenance will not only extend the lifespan of your well pump but also ensure a consistent water supply for your home.
Troubleshooting Well Pump Issues
Figuring out why your well pump is not turning on can be a complex task. Understanding common issues can help you diagnose the problem. Let’s dive into crucial checks and troubleshooting steps.
Checking Electrical Connections
Ensuring the electrical connections to your well pump are intact is the first step.
- Blown Fuses and Tripped Breakers: Check your circuit breaker for any tripped switches or blown fuses. This is often a quick and straightforward fix.
- Corroded Splice Connections: Inspect the splice connections for any signs of corrosion. Corroded connections can interrupt the power supply to the pump (R.C. Worst & Company Inc.).
- Voltage Check: Ensure that the voltage is within +/- 10% of the motor rating. Verify the power at various components like the pressure switch and control box (R.C. Worst & Company Inc.).
You might find further details about troubleshooting electrical issues in our article on troubleshooting well pump problems.
Submersible Pump Troubleshooting
If you have a submersible well pump, specific issues might arise that require detailed attention.
- Nonstop Pump Operation: If the pump keeps running, it could be due to problems such as a broken water line, a faulty check valve, or issues with the well casing. Hearing clicking sounds from the pressure switch without water flow could indicate these problems (Family Handyman).
Issue | Possible Cause | Action Required |
---|---|---|
Nonstop Operation | Broken water line, bad check valve | Hire a professional |
When dealing with a constantly running pump, you might want to explore our guide on well pump keeps running.
Pressure Switch Examination
The pressure switch is a vital component of your well pump system.
- Inspect for Wear and Defects: Examine the pressure switch for any signs of wear or defects. This switch is crucial for the system to function correctly.
Symptom | Inspection Point | Solution |
---|---|---|
Erratic Pressure | Pressure Switch | Replace the switch |
Detailed instructions on this process can be found in our article on replacing well pump pressure switch.
Addressing these key areas can help you get to the root of why your well pump is not turning on. If more detailed work or replacements are needed, consulting a professional or further reading on our other relevant articles will be beneficial. For more signs of potential pump problems, visit signs of well pump failure.
Signs of Well Pump Problems
Often, the first signs of well pump issues manifest long before the system stops working entirely. For homeowners, recognizing these indicators can help in addressing problems early. Here are some common signs of well pump problems.
Constant Running Pumps
If your well pump runs nonstop, it typically indicates an underlying issue that needs immediate attention. Persistent pump operation can be due to several reasons (Family Handyman):
- No water flow
- Broken water line from the well to the house
- Bad check valve
- Faulty connector
- Broken water line inside the well casing
It’s recommended to hire a professional to diagnose and fix the problem, as continuous running can lead to significant wear and tear on the pump. For further guidance, see our in-depth article on well pump keeps running.
Pressure Tank Troubles
Issues with the pressure tank can also affect how your well pump operates. Common symptoms of pressure tank problems include fluctuating water pressure, odd noises, and a continuously running pump. The pressure tank’s role is to maintain system pressure and provide a buffer to reduce pump cycling. Examine whether the pressure tank has the correct air charge, as an imbalance could directly impact pump functionality.
Problem | Indicator |
---|---|
Low Water Pressure | Fluctuating water pressure, no water flow |
Faulty Pressure Switch | Clicking sounds, constant running pump |
Air Charge Issues | Cycling pump, inconsistent pressure |
For troubleshooting tips on adjustments and replacements, refer to our articles on adjusting well pump pressure switch and replacing well pump pressure switch.
Pump Lifespan Expectancy
Understanding the lifespan of your well pump can help in preemptive maintenance and planning for eventual replacement. On average, well pumps last between 8 to 15 years, though some may extend beyond two decades (Fresh Water Systems).
Pump Type | Average Lifespan (years) |
---|---|
Submersible Pump | 8 – 10 |
Jet Pump | 10 – 15 |
Centrifugal Pump | 15 – 20 |
Symptoms indicating the need for replacement involve:
- Low water pressure
- Constant running
- Frequent electrical issues
Effective maintenance and timely inspections can prolong the life of your pump. For cost-related information, check our article on cost to replace well pump and for troubleshooting steps visit troubleshooting well pump problems.
By recognizing these signs early, you can address well pump issues proactively, ensuring a reliable water supply for your home.
CONTACT US TODAY

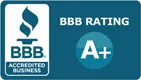

As Seen & Heard On
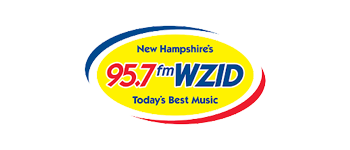
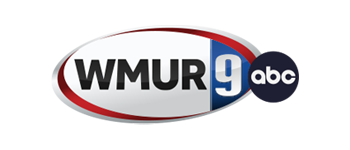

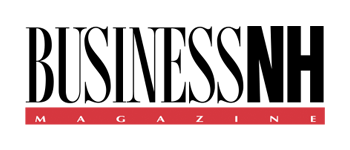
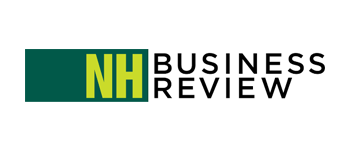
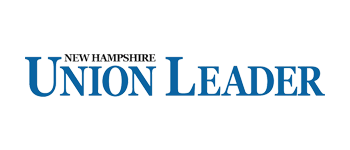
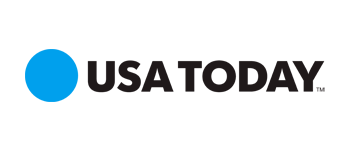
Reach Out to Our Team for More Details
Feel free to call Sanford Temperature Control or fill out the online form for more information. You may also get in touch with our team to schedule an appointment. We look forward to hearing from you.